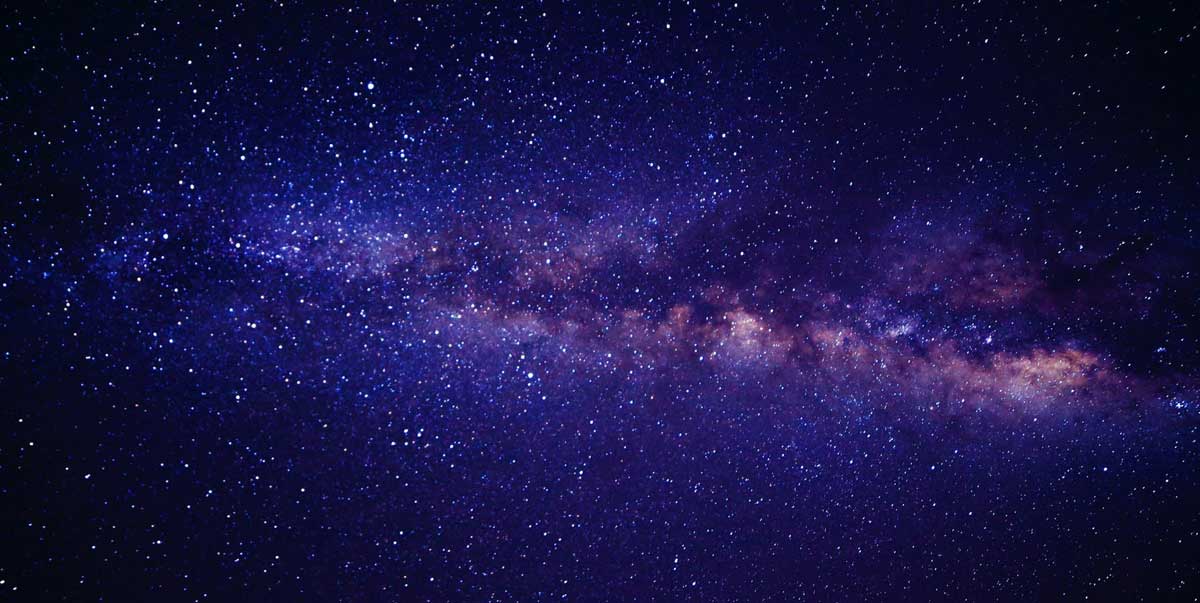
HVAC-PFEER Calculation in Excel
PFEER stands for the “Prevention of Fire, Explosion, and Emergency Response” regulations, which apply to workplaces where flammable or explosive substances are present. HVAC systems can be potential sources of ignition and therefore must be designed, installed, operated, and maintained in compliance with PFEER regulations to prevent fire, explosion, or other emergency situations.
To ensure compliance with PFEER regulations, HVAC systems must undergo regular inspection and maintenance by qualified professionals who are familiar with the specific requirements of PFEER. This includes ensuring that HVAC equipment and installations are properly designed and constructed, that the system is operated within its safe operating limits, and that proper emergency response procedures are in place in the occurrence of a fire or explosion.
Additionally, it is important to ensure that all personnel who work with or around HVAC equipment are properly trained in PFEER regulations and emergency response procedures, and are aware of the potential hazards associated with the equipment and substances used in the system.
Other HVAC Integrity tests:
To ensure that HVAC modules function properly and maintain air quality, it is essential to perform integrity tests.
Integrity tests are a series of tests that verify the performance of HVAC modules. These tests are performed to ensure that the modules meet the required standards for air quality, temperature control, and energy efficiency. The following are some of the most common HVAC module integrity tests:
HVAC Airflow Integrity Testing:
Airflow testing is a critical component of HVAC module integrity testing. This test is used to verify that the HVAC module can deliver the required amount of airflow to maintain the desired temperature and air quality in the building. Airflow testing measures the rate of airflow, air velocity, and static pressure inside the HVAC module.
There are several methods of performing airflow testing, but the most common method is using an airflow hood or capture hood. An airflow hood is a specialized device that is placed over a register or grille to measure the airflow rate. The device contains a series of sensors that measure the velocity of the air entering or leaving the HVAC module. The velocity measurements are then used to calculate the airflow rate.
To perform airflow testing, the technician places the airflow hood over the register or grille and adjusts the sensors to measure the airflow rate. The technician may need to adjust the airflow damper to achieve the desired airflow rate. The airflow rate is typically measured in cubic feet per minute (CFM) or cubic meters per hour (m3/h).
In addition to measuring airflow rate, airflow testing also measures air velocity and static pressure. Air velocity is the speed of the air as it enters or leaves the HVAC module, and it is measured in feet per minute (FPM) or meters per second (m/s). Static pressure is the force exerted by the air on the walls of the HVAC module and is measured in inches of water column (in. WC) or pascals (Pa).
Once the airflow testing is complete, the technician will analyze the results to ensure that the HVAC module is delivering the required amount of airflow. If the airflow rate is too low, the technician may need to adjust the airflow damper or inspect the ductwork for obstructions. If the airflow rate is too high, the technician may need to adjust the airflow damper or inspect the ductwork for leaks.
HVAC Leak Integrity Testing:
Leak testing is an essential part of HVAC systems’ installation and maintenance processes. It is performed to ensure that there are no leaks in the system that could lead to energy waste, decreased efficiency, and potential safety hazards.
There are different methods of leak testing in HVAC systems, and the choice of method depends on the type of system, its size, and the specific requirements of the project. Here are some of the most common leak testing methods used in HVAC:
ServiceFolder's Field Service Management Software provides complete software solutions for back office and field service technicians for the HVAC Businesses.
Bubble Test:
The bubble test is a simple and inexpensive leak testing method that involves applying a soap solution to the areas where leaks are suspected. If there is a leak, the solution will form bubbles in the affected area. This method is often used for smaller HVAC systems or for identifying leaks in specific areas.
Pressure Test:
The pressure test is a more comprehensive method that involves pressurizing the HVAC system with air or nitrogen and monitoring the pressure for a specified period. The pressure will decrease in the event of a leak, revealing its position. This method is commonly used for larger HVAC systems.
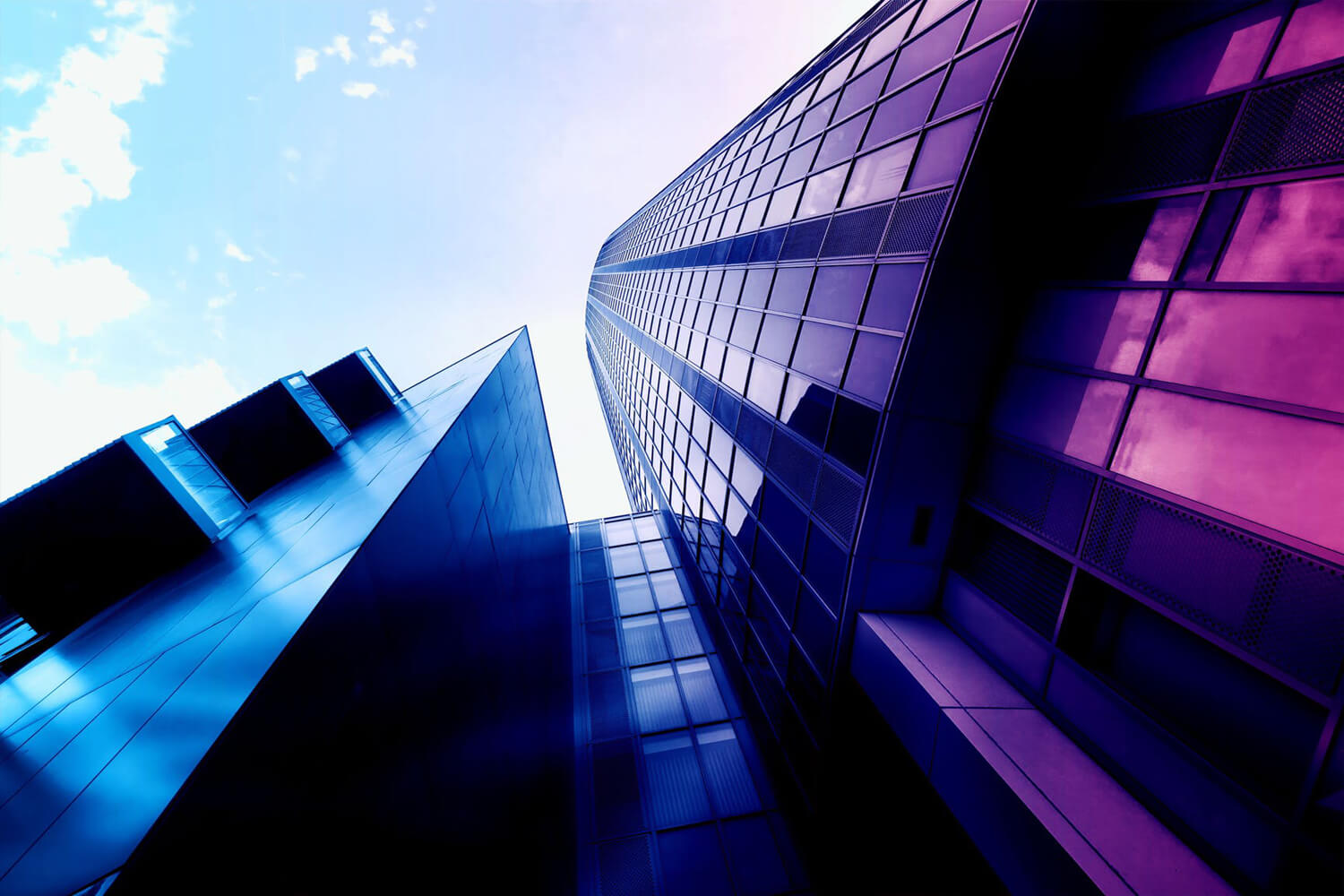
Ultrasonic Test:
The ultrasonic test uses high-frequency sound waves to detect leaks in HVAC systems. The equipment used for this method converts the sound waves into audible signals that can be detected by the operator. This method is useful for detecting leaks in hard-to-reach areas or for systems that contain refrigerants or other gases.
Gas Tracer Test:
The gas tracer test involves introducing a trace gas into the HVAC system and monitoring its concentration to detect leaks. The gas used for this test is typically a non-toxic, non-flammable, and non-reactive gas, such as nitrogen or helium. This method is commonly used for larger HVAC systems or those that use refrigerants.
HVAC Performance Integrity Testing:
Performance testing on HVAC systems is crucial for maintaining their efficiency and ensuring that they are operating at their best capacity. It is performed to ensure that the HVAC system is functioning efficiently and effectively and to identify any potential issues that may require repair or adjustment.
There are different types of performance testing methods used in HVAC systems, and the choice of method depends on the type of system, its size, and the specific requirements of the project. Here are some of the most common performance testing methods used in HVAC:
Get started with ServiceFolder
- Manage Jobs & Staff
- On Site Quote and Invoice
- On Site Notes and Photos
- Sync with Quickbooks Online
- Print Designer for all Documents
- Equipment/Asset Management
- Customer Management
- Leads Management
- Inventory Management
- Customer Notifications
- Customer Fields
- PriceBooks
Airflow Testing:
Airflow testing measures the volume of air that the HVAC system can move through the ductwork and into the space it is designed to condition. This test is performed using specialized equipment, such as a flow hood or an anemometer, and the results are compared to the system’s design specifications to ensure that it is working efficiently.
Temperature Testing:
Temperature testing measures the temperature of the air as it enters and exits the HVAC system. This test is performed using specialized thermometers or temperature probes, and the results are compared to the system’s design specifications to ensure that it is delivering the correct temperature to the conditioned space.
Try all in one HVAC Businesses Software - Free - 1 UserHumidity Testing:
Humidity testing measures the level of moisture in the air that the HVAC system is conditioning. This test is performed using specialized equipment, such as a psychrometer or a humidity sensor, and the results are compared to the system’s design specifications to ensure that it is maintaining the correct level of humidity in the conditioned space.
Energy Efficiency Testing:
Energy efficiency testing measures the HVAC system’s energy consumption and efficiency. This test is performed using specialized equipment, such as a wattmeter or an energy analyzer, and the results are compared to the system’s design specifications to ensure that it is operating at optimal efficiency.
HVAC Control Integrity Testing:
The purpose of control testing is to ensure that the HVAC control systems are operating as intended and that they are effectively managing the HVAC equipment to maintain a comfortable and healthy environment. Here are some of the most common control testing methods used in HVAC systems:
Functional Testing:
Functional testing involves testing the individual components of the HVAC control system, such as thermostats, sensors, actuators, and controllers, to ensure that they are working as intended. This test is performed using specialized equipment, such as a multimeter or an oscilloscope, and the results are compared to the system’s design specifications to identify any issues that may require repair or adjustment.
The sequence of Operation Testing:
The sequence of operation testing involves testing the entire HVAC control system to ensure that it is operating in the correct sequence and that all components are working effectively together. This test is performed using specialized software or tools, and the results are compared to the system’s design specifications to ensure that the system is operating as intended.
Load Testing:
Load testing involves testing the HVAC control system under different load conditions, such as different outside temperatures, to ensure that it is able to maintain a comfortable and healthy environment. This test is performed using specialized equipment, such as a load bank or a variable frequency drive, and the results are compared to the system’s design specifications to ensure that it is operating efficiently and effectively under different load conditions.
HVAC Noise testing:
Performing regular noise testing on HVAC systems is crucial for ensuring that the noise level generated by the HVAC equipment and systems is within acceptable limits and does not cause discomfort or disturbance to the building’s occupants. Here are some of the most common noise testing methods used in HVAC systems:
Sound Level Testing:
Sound level testing involves measuring the sound level generated by the HVAC equipment and systems using specialized equipment, such as a sound level meter. The results are compared to industry standards and building codes to ensure that the noise level is within acceptable limits.
Octave Band Analysis:
Octave band analysis involves breaking down the sound level into different frequency bands using specialized equipment, such as an octave band analyzer. This test is useful for identifying specific noise sources and frequencies that may be causing excessive noise levels in the conditioned space.
Sound Transmission Testing:
Sound transmission testing involves measuring the sound transmission through building partitions, such as walls and floors, to determine the extent to which HVAC noise is being transmitted between different areas of the building. This test is performed using specialized equipment, such as a sound transmission class (STC) meter.
Conclusion:
HVAC module integrity tests are essential to ensuring that HVAC systems in buildings operate efficiently and maintain good indoor air quality. These tests verify the performance, integrity, and functionality of the HVAC module and control system. By performing these tests, building owners and operators can ensure that their HVAC systems meet the required standards for air quality, temperature control, and energy efficiency.
FAQ
What is HVAC PFEER calculation?
HVAC PFEER calculation stands for Heating, Ventilation, Air Conditioning (HVAC) Pressurization, Filtration, and External Entry Rate (PFEER) calculation. It is a method used to determine the ventilation requirements for a space to maintain a safe and healthy environment by controlling the entry of contaminants from outside.
Why is HVAC PFEER calculation important?
HVAC PFEER calculation is important because it ensures that the ventilation system of a building is designed and operated in a way that protects occupants from exposure to harmful contaminants, such as airborne viruses, bacteria, and other pollutants. It also helps to prevent the spread of infectious diseases in buildings.
What factors are considered in HVAC PFEER calculation?
HVAC PFEER calculation considers factors such as the number of occupants in the space, the size of the space, the outdoor air quality, the type and efficiency of the ventilation system, the filtration efficiency, and the rate of air exchange.
How is HVAC PFEER calculation performed?
HVAC PFEER calculation is performed using a mathematical formula that takes into account the factors mentioned above. The formula calculates the minimum ventilation rate required to maintain a safe and healthy environment in the space.
Who should perform HVAC PFEER calculation?
HVAC PFEER calculation should be performed by a qualified HVAC engineer or consultant who has experience in designing and operating ventilation systems for buildings. It is important to ensure that the calculations are accurate to ensure the safety and health of building occupants.
What are the benefits of performing HVAC PFEER calculation?
The benefits of performing HVAC PFEER calculation include ensuring the safety and health of building occupants, reducing the risk of the spread of infectious diseases, improving indoor air quality, and reducing energy costs by optimizing the operation of the ventilation system.
What are the consequences of not performing HVAC PFEER calculation?
The consequences of not performing HVAC PFEER calculation can be severe, including the spread of infectious diseases among building occupants, poor indoor air quality, and increased energy costs due to inefficient operation of the ventilation system. In addition, failure to comply with building codes and regulations regarding ventilation can result in legal and financial consequences.

Try Now
ServiceFolder's field service scheduling software free plan is perfect for small businesses with up to three people or less. It includes time tracking, scheduling, and mobile app features that make it one of the best mobile field service management software solutions for small businesses available. It is perfect for any small business company within the field service industry that wants to use technology to increase performance and productivity.