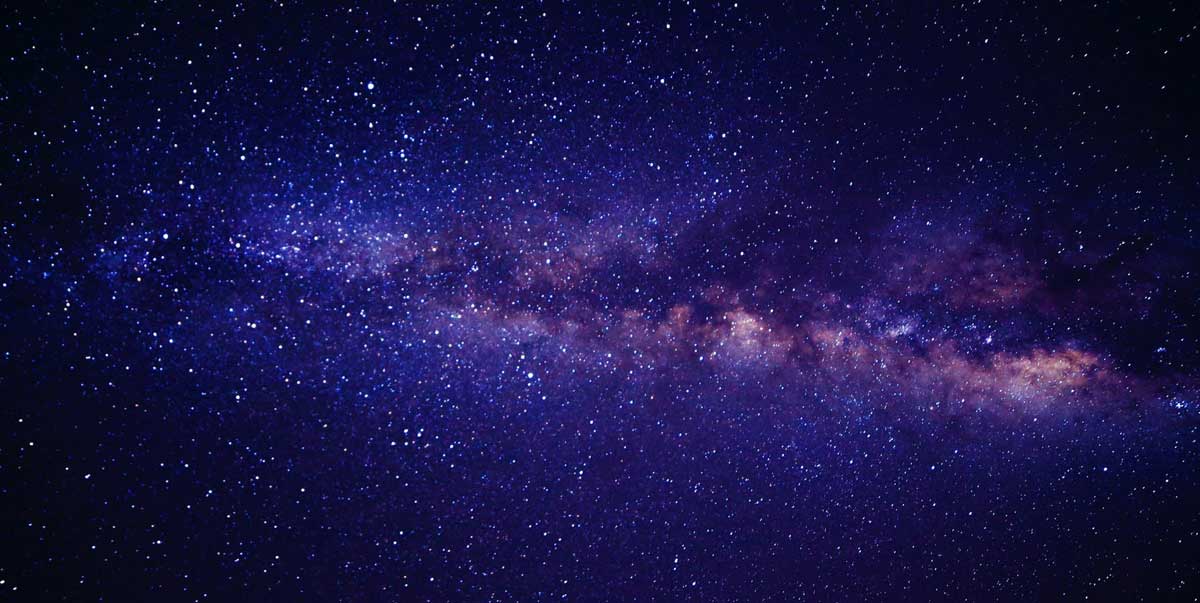
Equipment Tracking Software for Paving Field Service Business
As a paving field service business owner, you’re likely no stranger to the frustration of lost or misplaced equipment, or the financial burden that comes with it. You’ve probably spent countless hours searching for missing gear, only to find it hidden in plain sight or, worse, never to be seen again. But what if you could say goodbye to those costly delays and hello to increased productivity? With equipment tracking software, you can do just that. But how does it work, and what features do you need to look for to get the most out of your investment?
ServiceFolder's Field Service Management Software provides complete software solutions for back office and field service technicians for the Paving Businesses.
Key Takeaways
• Implement equipment tracking software to reduce downtime and increase productivity in paving field service businesses. • Real-time tracking and alerts enable proactive issue management, minimizing equipment breakdowns and reducing repair costs. • Automated reporting and analytics provide insights into equipment usage and performance, helping businesses optimize resource allocation. • GPS tracking devices pinpoint exact equipment location, reducing manual checks and improving asset utilization and security. • Customizable alerts and notifications ensure timely maintenance scheduling, extending equipment lifespan and reducing replacement costs.
Benefits of Equipment Tracking
By implementing equipment tracking software, you can greatly reduce downtime and increase productivity, resulting in improved overall efficiency and profitability for your paving business.
This is because you’ll have real-time visibility into the location and status of your equipment, allowing you to quickly identify and address any issues that may be causing delays.
With equipment tracking software, you can also optimize your equipment allocation, ensuring that the right machines are assigned to the right jobs and that you’re not over- or under-allocating resources.
Additionally, you’ll be able to track maintenance schedules and perform routine checks more efficiently, reducing the likelihood of breakdowns and extending the lifespan of your equipment.
By streamlining your operations in this way, you can free up more time and resources to focus on growing your business and taking on new projects.
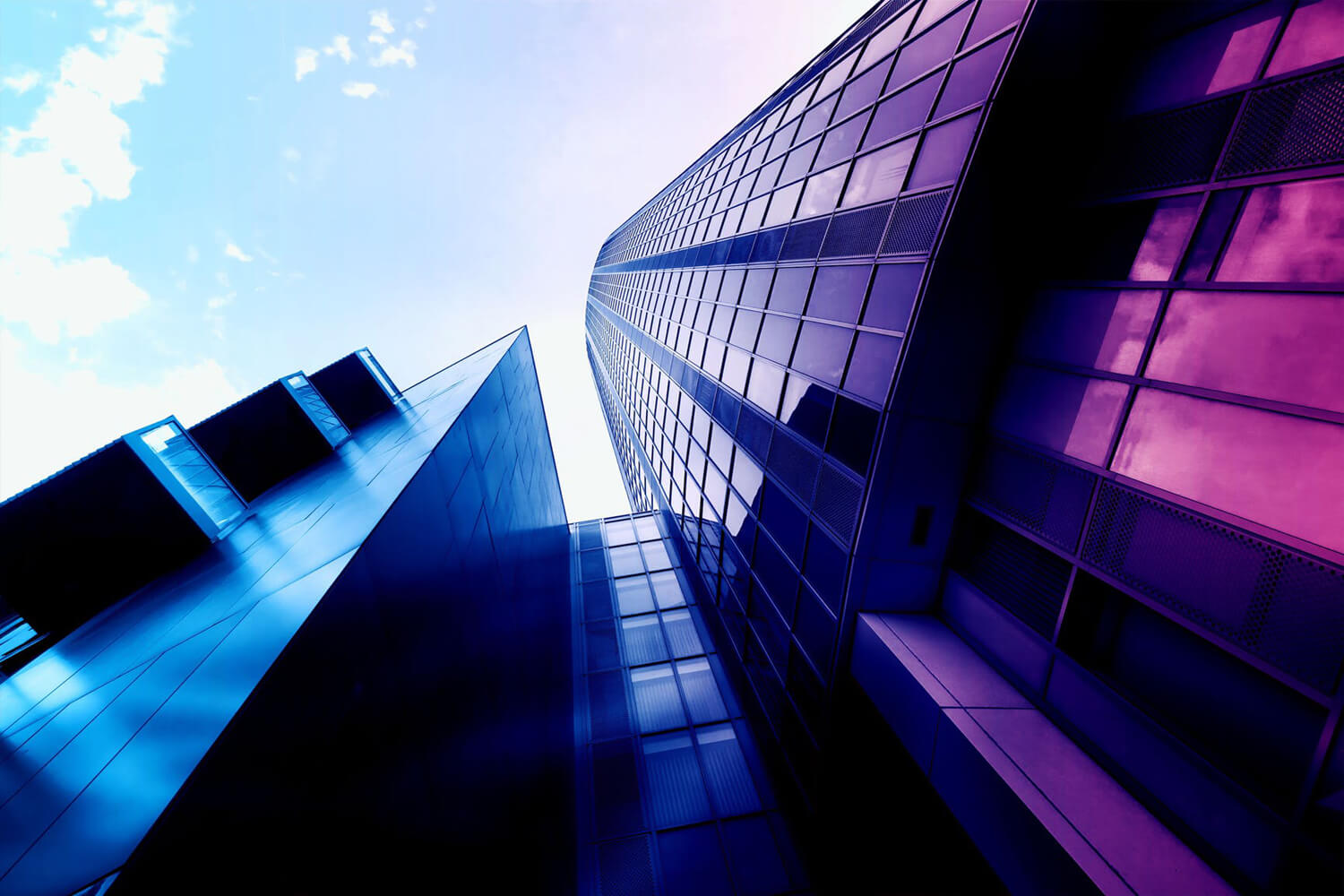
Key Features to Look For
When selecting an equipment tracking software for your paving business, you’ll want to prioritize features that provide actionable insights, automate routine tasks, and integrate seamlessly with your existing operations.
You should look for a system that can track equipment location, status, and maintenance history in real-time. This will allow you to make informed decisions about equipment deployment, reduce downtime, and optimize maintenance schedules. Additionally, consider a software that offers customizable alerts and notifications, allowing you to stay on top of equipment issues before they become major problems.
Another key feature to look for is automated reporting and analytics. This will help you identify trends and patterns in equipment usage, allowing you to optimize your operations and reduce costs.
You should also verify that the software is user-friendly and accessible on-the-go, so your team can stay connected and informed in the field.
Finally, consider a system that integrates with your existing accounting and inventory management systems, guaranteeing a streamlined and efficient workflow.
How GPS Tracking Works
How do you harness the power of GPS tracking to monitor your paving equipment’s every move?
With GPS tracking, you can pinpoint the exact location of your equipment in real-time, eliminating the need for manual checks and reducing the risk of theft or loss.
Here’s how it works: a small GPS device is installed on your equipment, which sends location data to the cloud via cellular or satellite connectivity. This data is then transmitted to your tracking software, where you can view the location of your equipment on a map, receive alerts for unusual activity, and analyze usage patterns.
Some key benefits of GPS tracking include:
-
Improved asset utilization: Verify your equipment is being used efficiently and effectively.
-
Enhanced security: Receive alerts for unauthorized movement or tampering.
-
Increased productivity: Optimize your equipment deployment and reduce downtime.
Get started with ServiceFolder
- Manage Jobs & Staff
- On Site Quote and Invoice
- On Site Notes and Photos
- Sync with Quickbooks Online
- Print Designer for all Documents
- Equipment/Asset Management
- Customer Management
- Leads Management
- Inventory Management
- Customer Notifications
- Customer Fields
- PriceBooks
Asset Management Best Practices
You can maximize your return on investment in equipment tracking software by implementing asset management best practices that streamline your operations and extend the lifespan of your paving equipment. By doing so, you’ll be able to make data-driven decisions, reduce downtime, and increase productivity.
Start by assigning a unique identifier to each piece of equipment, making it easier to track and maintain. Regularly inspect and maintain your equipment to prevent unexpected breakdowns. Implement a preventive maintenance schedule to guarantee routine checks and repairs are performed on time.
You should also establish a clear system for reporting and addressing equipment issues, ensuring that problems are addressed promptly and efficiently. Additionally, keep accurate records of equipment history, including maintenance, repairs, and upgrades.
Common Pain Points Solved
By implementing equipment tracking software and asset management best practices, paving businesses can overcome common pain points that hinder their operations, such as equipment loss, theft, or misplacement.
You no longer have to worry about the financial burden of replacing lost or stolen equipment or the downtime it causes. With equipment tracking software, you can pinpoint the exact location of your assets, reducing the likelihood of loss or theft.
Additionally, you’ll experience improved operational efficiency and reduced administrative burdens. You’ll no longer need to manually track equipment locations, freeing up staff to focus on more critical tasks.
This means you can:
-
Reduce equipment downtime and increase productivity
-
Improve maintenance scheduling and reduce repair costs
-
Enhance customer satisfaction with faster response times and more efficient job completions
Real-Time Data and Analytics
Equipment tracking software provides your paving business with real-time data and analytics, giving you a bird’s eye view of your entire operation and empowering data-driven decision making. With real-time insights, you can identify areas of improvement, optimize resource allocation, and streamline your operations.
Here’s a breakdown of the types of real-time data and analytics you can expect from equipment tracking software:
Data Point | Benefits |
---|---|
Equipment Location | Identify idle equipment, reduce theft, and optimize deployment |
Equipment Performance | Monitor usage patterns, detect potential issues, and schedule maintenance |
Operator Performance | Evaluate operator efficiency, identify training opportunities, and improve accountability |
Maximizing ROI With Equipment Tracking
With real-time data and analytics in hand, paving business owners like yourself can now focus on maximizing their return on investment (ROI) by making informed decisions that drive profitability and growth.
By leveraging equipment tracking software, you can identify areas of improvement, enhance operations, and make data-driven decisions to increase revenue.
Here are some ways you can maximize your ROI with equipment tracking:
-
Reduce equipment downtime: By tracking equipment performance and maintenance schedules, you can minimize downtime and guarantee that your equipment is always running at peak levels, reducing revenue lost due to equipment failure.
-
Enhance equipment allocation: With real-time data on equipment usage, you can allocate your equipment more efficiently, guaranteeing that the right equipment is deployed to the right job, and reducing waste.
-
Improve labor productivity: By tracking equipment usage and performance, you can identify opportunities to improve labor productivity, reducing labor costs and increasing revenue.
Frequently Asked Questions
Can Equipment Tracking Software Integrate With Existing Fleet Management Systems?
When considering software to track your equipment, you’ll want to know if it can sync with your existing fleet management systems. Fortunately, most equipment tracking software can integrate seamlessly, allowing you to access all your data in one place.
How Does Equipment Tracking Software Handle Equipment Rented or Leased to Others?
You’re wondering how equipment tracking software handles equipment rented or leased to others? Well, most software allows you to create separate profiles for rented/leased equipment, tracking usage, and generating reports for billing and maintenance purposes.
Are There Any Equipment Tracking Software Options for Small Fleets or Businesses?
You’ll find equipment tracking software options suitable for small fleets or businesses, offering flexible pricing plans and scalable features that adapt to your growing needs, without breaking the bank or overwhelming your operations.
Do Equipment Tracking Systems Comply With Industry-Specific Regulations?
You’ll find that many equipment tracking systems comply with industry-specific regulations, such as OSHA, EPA, and DOT, ensuring you meet standards for safety, environmental sustainability, and operational efficiency.
Can Equipment Tracking Software Be Used for Non-Powered Equipment and Tools?
You’re wondering if tracking software can monitor non-powered equipment and tools. Yes, you can use it to track anything with a unique identifier, from ladders to hand tools, helping you stay organized and efficient.
Conclusion
You’ve got the tools to revolutionize your paving field service business with equipment tracking software.
By automating reports, scheduling maintenance, and receiving customizable alerts, you’ll minimize downtime and optimize resource allocation.
With real-time visibility into equipment location and status, you’ll make data-driven decisions that boost productivity and maximize ROI.
It’s time to take control of your equipment and access the full potential of your business - start tracking today!
Disclaimer: Some information is provided through AI. Users should always conduct their own research and consult with qualified professionals before making any decisions.Affiliate information declaration: We may earn revenue from the products referred on this page and participate in affiliate programs.Related Posts

Try Now
ServiceFolder's field service scheduling software free plan is perfect for small businesses with up to three people or less. It includes time tracking, scheduling, and mobile app features that make it one of the best mobile field service management software solutions for small businesses available. It is perfect for any small business company within the field service industry that wants to use technology to increase performance and productivity.