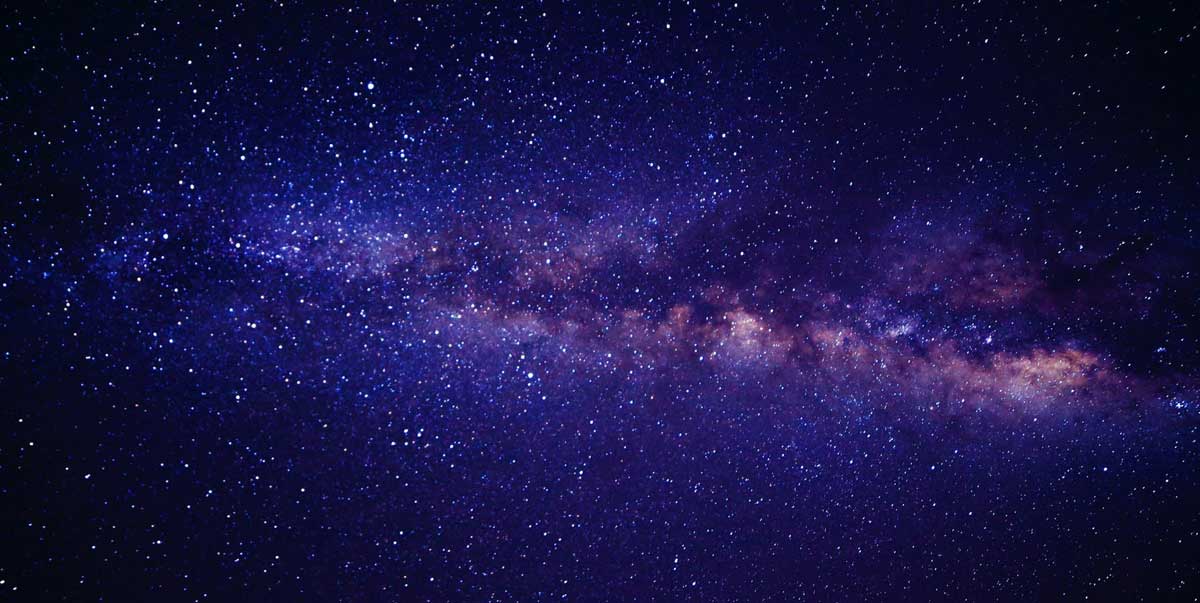
Equipment Tracking Software for Handyman Field Service Business
As a handyman field service business owner, you’re no stranger to the frustration of wasted time and resources due to misplaced or stolen equipment. You’ve likely spent hours searching for that one specific drill or tool, only to find it was left at the previous job site. But what if you could eliminate that stress and instead focus on growing your business? Equipment tracking software can be a game-changer, providing real-time visibility into your equipment’s location and status. But how do you get started, and what features do you need to look for in a tracking solution?
ServiceFolder's Field Service Management Software provides complete software solutions for back office and field service technicians for the Handyman Businesses.
Key Takeaways
• Implementing equipment tracking software reduces search time, allowing handymen to focus on tasks and increase productivity. • Accurate records of equipment usage and location lower the risk of theft and misplacement, saving the business money. • Real-time tracking updates and customizable reporting provide insights into equipment usage, enabling data-driven operational decisions. • Integration with existing field service management tools streamlines operations, and user-friendly interfaces minimize training time. • Automating equipment management through tracking software results in significant long-term cost savings and substantial ROI for the business.
Benefits of Equipment Tracking
By implementing equipment tracking software, you’ll be able to keep tabs on your tools and machinery, saving time and resources that would otherwise be wasted on searching for misplaced items. This means you can allocate more time to actual work, increasing your productivity and ultimately, your revenue.
With accurate records of equipment locations, you can also reduce the risk of theft and loss. You’ll know exactly who had the tool last, when it was used, and where it’s supposed to be.
Moreover, equipment tracking software helps you stay on top of maintenance schedules. You’ll receive notifications when equipment is due for servicing, ensuring it remains in good working condition and reducing the likelihood of breakdowns. This not only saves you money on repair costs but also prevents delays in your projects.
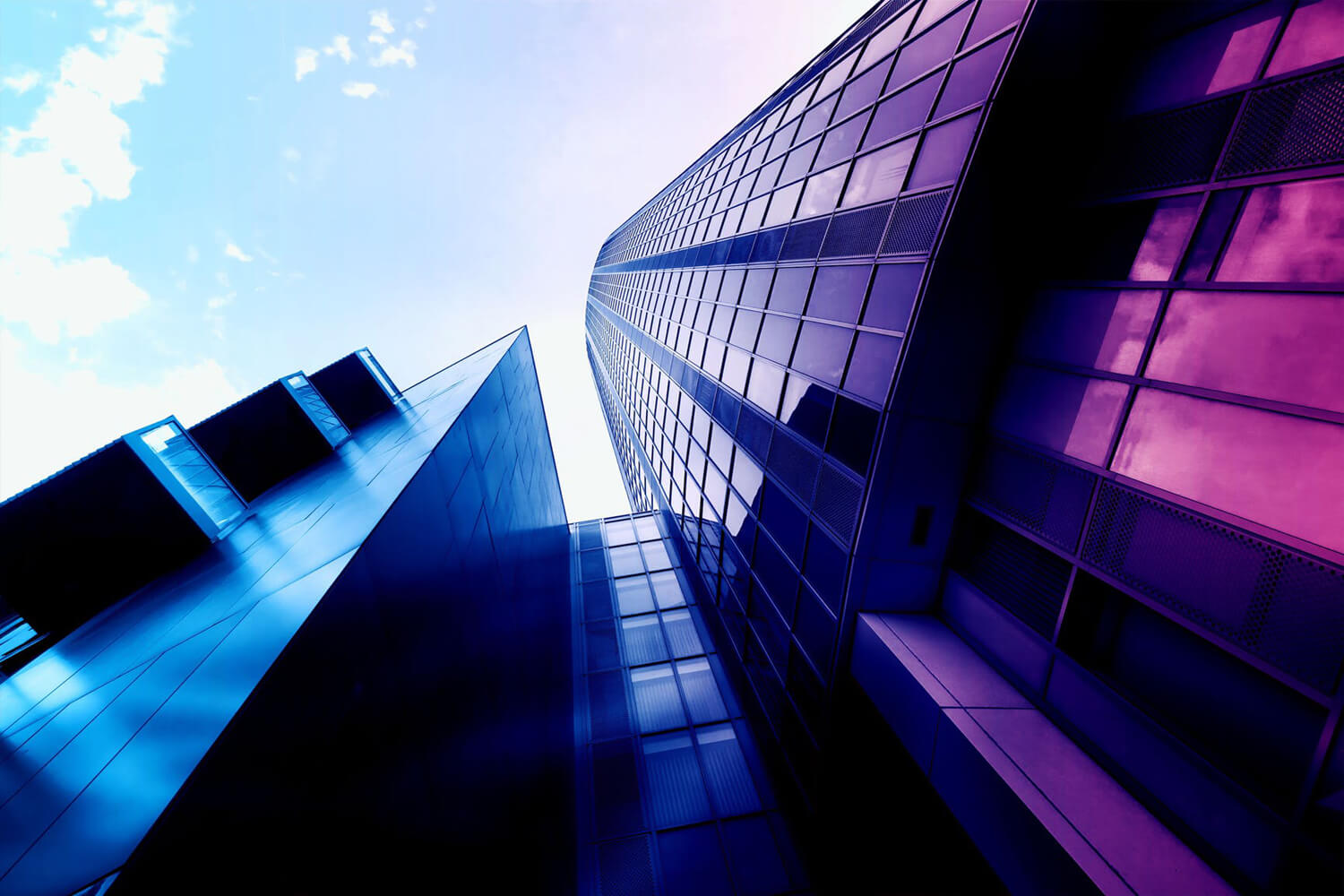
How Equipment Tracking Software Works
Now that you’ve seen the benefits of equipment tracking software, let’s take a closer look at how it actually works.
At its core, the software is a centralized system that helps you monitor and manage your equipment across various locations and jobsites. You can create a digital inventory of your equipment, including tools, machinery, and vehicles, and assign unique identifiers to each item.
This allows you to track their movement, location, and status in real-time. When an item is checked out or moved, the software updates its location and status, ensuring that you always know where your equipment is and who’s using it.
You can also set reminders for maintenance, calibration, and inspections, ensuring that your equipment is always in good working condition.
With equipment tracking software, you can generate reports and analytics to identify trends, optimize your operations, and make data-driven decisions.
Features to Look for in Software
When selecting an equipment tracking software for your handyman business, you’ll want to look for features that cater to your specific needs and workflow. A key feature to take into account is asset categorization, which allows you to group and organize your equipment by type, location, or status. This guarantees you can quickly locate specific tools or equipment when you need them.
Another essential feature is real-time tracking, which enables you to monitor the location and status of your equipment in real-time. This helps prevent loss or theft and guarantees you can respond quickly to changes in your equipment’s status.
You should also look for software that offers customizable reporting and analytics, which can provide valuable insights into equipment usage and maintenance needs.
Additionally, think about software that integrates with your existing field service management tools, such as scheduling and invoicing software. This streamlines your operations and reduces manual data entry.
Get started with ServiceFolder
- Manage Jobs & Staff
- On Site Quote and Invoice
- On Site Notes and Photos
- Sync with Quickbooks Online
- Print Designer for all Documents
- Equipment/Asset Management
- Customer Management
- Leads Management
- Inventory Management
- Customer Notifications
- Customer Fields
- PriceBooks
Choosing the Right Tracking Solution
Evaluate your handyman business’s specific needs and workflow to determine the best equipment tracking solution for your operation. You know your business inside and out, so think about what you need the software to do.
Do you have a large inventory of equipment that’s frequently moved between job sites? Do you need to track equipment maintenance and repair schedules? Are there specific reporting or analytics requirements you need to meet? Make a list of your must-haves and nice-to-haves to guide your search.
Next, research different equipment tracking solutions and read reviews from other handyman businesses. Look for case studies or testimonials that demonstrate how the software has helped similar businesses.
Consider factors like scalability, customization options, and integrations with other tools you use. You may also want to ask about customer support and training resources.
Implementation and Onboarding Process
You’ve selected the perfect equipment tracking software for your handyman business, and it’s time to get it up and running. Now, it’s vital to focus on the implementation and onboarding process to guarantee a seamless changeover.
Start by designating a team leader or administrator to oversee the setup and training process. This person will be responsible for configuring the software, setting up user accounts, and customizing the system to fit your business needs.
Next, schedule a training session with the software provider to walk you and your team through the system’s features and functionality. This will help you understand how to track equipment, manage maintenance schedules, and generate reports. It’s also significant to develop a plan for data migration if you’re transferring existing equipment data into the new system.
During the onboarding process, take advantage of the software provider’s support resources, such as online tutorials, webinars, and customer support teams. These resources will help you troubleshoot any issues that arise and guarantee you’re getting the most out of your equipment tracking software.
Try all in one Handyman Businesses Software - Free - 1 UserCommon Pain Points Solved by Tracking
By implementing equipment tracking software, you’ll eliminate the frustration of dealing with lost or misplaced tools, a problem that’s likely cost your handyman business time and money in the past.
You’ve probably spent hours searching for a specific drill or wrench, only to find it was misplaced or stolen. This not only wastes valuable time but also affects your bottom line.
With equipment tracking software, you’ll no longer have to deal with these issues. Here are some common pain points that tracking can solve:
-
Reducing tool theft: Keep track of who checked out which tools and when, making it easier to hold employees accountable for lost or stolen equipment.
-
Streamlining tool allocation: Easily assign tools to specific jobs or technicians, ensuring everyone has what they need to get the job done.
-
Minimizing downtime: Quickly locate missing tools or equipment, reducing the time spent searching and getting your technicians back to work faster.
-
Improving maintenance scheduling: Track equipment maintenance and receive alerts when it’s time for servicing, reducing equipment failure and extending its lifespan.
ROI and Long-Term Cost Savings
Implementing equipment tracking software can considerably boost your handyman business’s bottom line, as it helps you reap substantial long-term cost savings and a notable return on investment (ROI). By automating equipment management, you’ll reduce manual errors, minimize equipment loss, and optimize resource allocation. This means you’ll spend less on replacement costs, maintenance, and unnecessary purchases.
You’ll also see a significant reduction in labor costs. With automated tracking, you’ll quickly identify underutilized equipment and allocate it to other projects, reducing idle time and increasing productivity. Furthermore, equipment tracking software provides valuable insights into equipment performance, enabling you to schedule maintenance proactively and extend equipment lifespan.
In the long run, these cost savings will add up, resulting in a substantial ROI. You’ll be able to reallocate resources to other areas of your business, such as marketing, training, or expansion. By investing in equipment tracking software, you’re investing in the growth and profitability of your handyman business.
Frequently Asked Questions
Can Equipment Tracking Software Integrate With Existing Field Service Management Tools?
You wonder if software can sync with your existing tools. The good news is that many equipment tracking solutions can integrate seamlessly with your current field service management systems, streamlining your workflow and reducing errors.
How Do I Ensure Employee Buy-In for New Equipment Tracking Procedures?
You’ll want to communicate the benefits clearly, involve employees in the process, and provide training to guarantee a smooth changeover. Make sure they understand how the new procedures will make their jobs easier and more efficient.
Are There Any Equipment Tracking Software Options for Small Businesses or Solo Operators?
You’re looking for equipment tracking software options that fit your small business or solo operation. Yes, there are several affordable and user-friendly options available, including cloud-based solutions like TradeGecko, Zoho Inventory, and Sortly, which can streamline your equipment management.
Can Equipment Tracking Software Be Used for Rented or Leased Equipment?
You’re wondering if you can use equipment tracking software for rented or leased gear. Yes, you can! Many software options allow you to add rented or leased equipment to your inventory, making it easy to manage and track.
Is Equipment Tracking Software Compliant With Industry-Specific Regulations?
You’ll find that most equipment tracking software is designed to be compliant with industry-specific regulations, such as OSHA, EPA, and DOT, ensuring you meet standards for safety, environmental responsibility, and transportation.
Conclusion
You’ve seen how equipment tracking software can revolutionize your handyman field service business.
By streamlining operations, reducing costs, and increasing revenue, it’s a must-have tool for success.
With the right software, you’ll never have to worry about lost tools or equipment again.
You’ll have more time to focus on what matters - delivering exceptional service to your customers.
Get ready to take your business to the next level with equipment tracking software.
Disclaimer: Some information is provided through AI. Users should always conduct their own research and consult with qualified professionals before making any decisions.Affiliate information declaration: We may earn revenue from the products referred on this page and participate in affiliate programs.Related Posts

Try Now
ServiceFolder's field service scheduling software free plan is perfect for small businesses with up to three people or less. It includes time tracking, scheduling, and mobile app features that make it one of the best mobile field service management software solutions for small businesses available. It is perfect for any small business company within the field service industry that wants to use technology to increase performance and productivity.