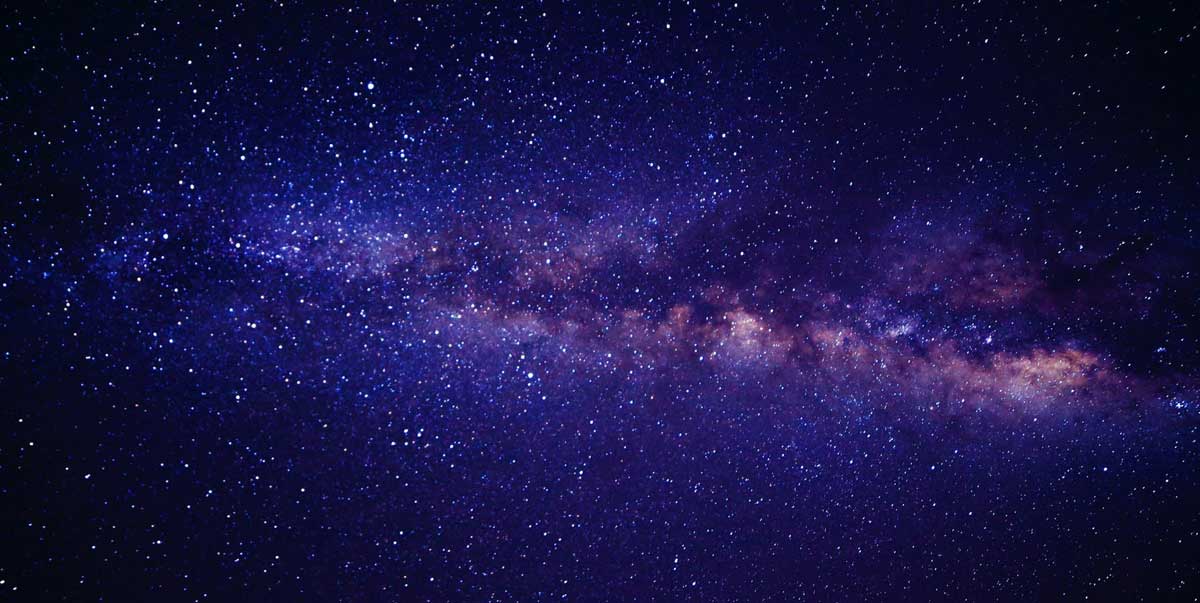
Equipment Tracking Software for Generator Maintenance Field Service Business
As a generator maintenance field service business owner, you understand the importance of keeping your equipment in top condition to guarantee timely service and customer satisfaction. But are you tired of dealing with manual tracking methods that lead to lost or misplaced equipment, delayed maintenance, and revenue losses? Implementing equipment tracking software can revolutionize your operations, providing real-time insights into your equipment’s location, status, and maintenance history. But what features should you look for in an equipment tracking software, and how can it specifically benefit your generator maintenance business?
ServiceFolder's Field Service Management Software provides complete software solutions for back office and field service technicians for the Generator Maintenance Businesses.
Key Takeaways
• Implementing equipment tracking software reduces generator downtime, increasing productivity and revenue potential for field service businesses. • Real-time location tracking and automated maintenance scheduling enable proactive issue identification and prompt response, minimizing troubleshooting time. • Customizable reporting and analytics provide valuable insights to optimize resource allocation, identify cost-reduction opportunities, and drive business growth. • Integration with existing tools like accounting and CRM systems streamlines operations, enhancing customer satisfaction and reputation. • Equipment performance analytics and data-driven decision-making enable field service businesses to uncover new service opportunities and improve overall efficiency.
Benefits of Equipment Tracking
By implementing equipment tracking software, you can greatly reduce equipment downtime and increase overall productivity, ultimately leading to cost savings and improved customer satisfaction.
This is because you’ll have real-time visibility into the location, status, and maintenance history of your generators. You’ll be able to quickly identify and address potential issues before they cause downtime, reducing the time your team spends on troubleshooting and repairs. This means you can schedule maintenance during slower periods, minimizing the impact on your operations.
With equipment tracking software, you’ll also be able to optimize your inventory management, ensuring you have the right parts and materials on hand when you need them. This will reduce delays and enable your team to complete jobs more efficiently.
As a result, you’ll be able to take on more jobs, increase revenue, and improve your reputation for reliability and responsiveness. By getting ahead of equipment maintenance, you’ll be able to focus on growing your business and delivering exceptional service to your customers.
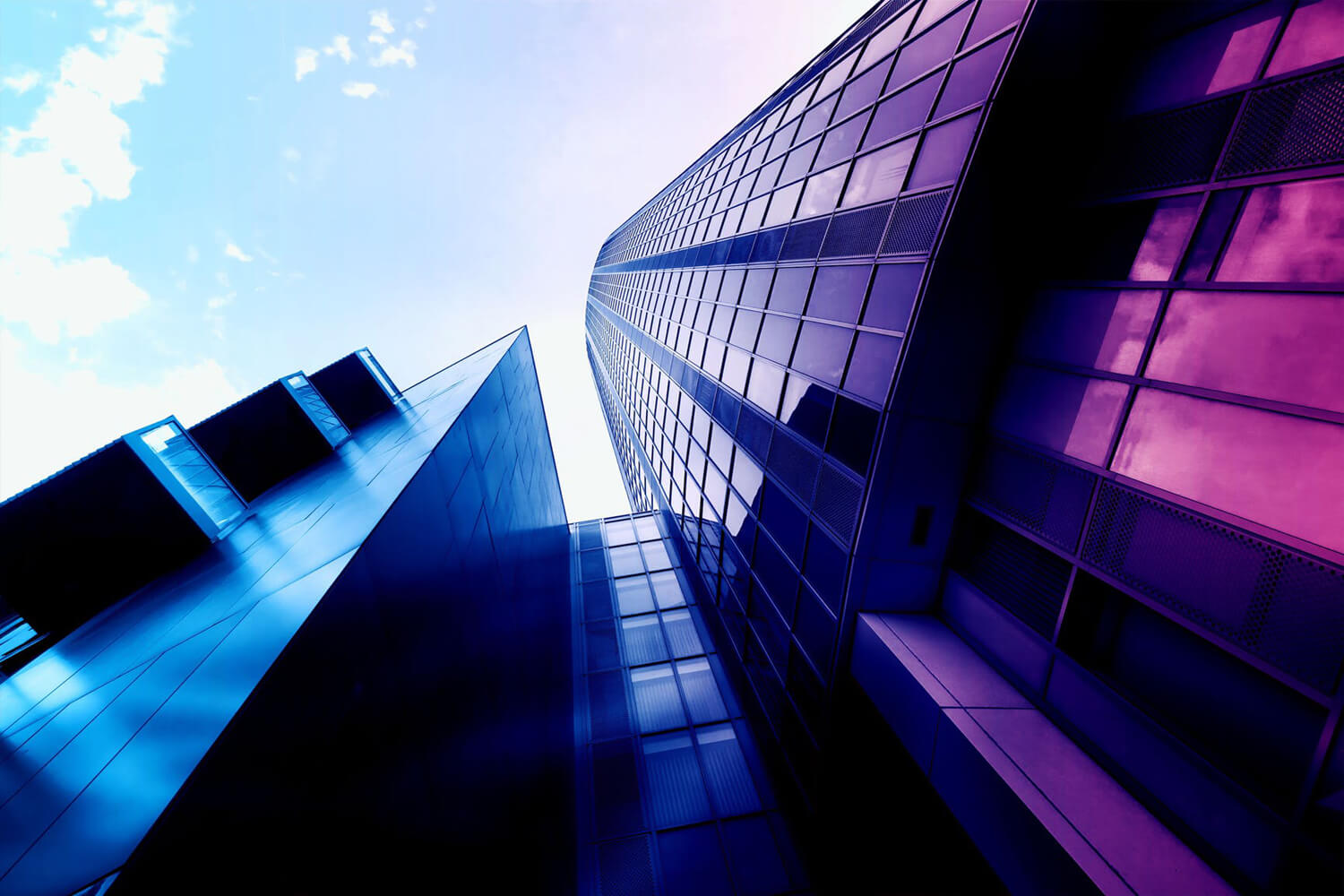
Discover more ServiceFolder Features for your
Generator Maintenance Businesses
Contact Us
Free - 1 User
Key Features to Look For
You’ll want to look for equipment tracking software that includes features like automated maintenance scheduling, real-time alerts, and customizable reporting to guarantee you’re getting the most out of your generator maintenance program.
These features will help you stay on top of maintenance tasks, respond quickly to issues, and make data-driven decisions.
Additionally, consider software that allows you to track equipment location, status, and history, as well as assign and manage work orders and technician tasks. This will give you a clear overview of your operations and help you optimize your workflow.
Moreover, look for software that integrates with other tools and systems you’re already using, such as accounting software or customer relationship management (CRM) systems. This will help you streamline your operations and reduce manual data entry.
Automating Maintenance Scheduling
Automating maintenance scheduling allows you to take a proactive approach to generator maintenance, ensuring that routine tasks are performed on time and reducing the risk of unexpected downtime.
With automated scheduling, you can set reminders for regular checks, oil changes, and other maintenance tasks, so you’ll never miss a critical deadline. This feature also enables you to allocate resources more efficiently, assigning the right technicians to the right jobs at the right time.
You can also prioritize tasks based on urgency and importance, focusing on the most critical maintenance needs first. Automated maintenance scheduling also helps you keep a record of all maintenance activities, enabling you to track equipment history and identify potential issues before they become major problems.
Get started with ServiceFolder
- Manage Jobs & Staff
- On Site Quote and Invoice
- On Site Notes and Photos
- Sync with Quickbooks Online
- Print Designer for all Documents
- Equipment/Asset Management
- Customer Management
- Leads Management
- Inventory Management
- Customer Notifications
- Customer Fields
- PriceBooks
Real-Time Location Tracking
With real-time location tracking, you can pinpoint the exact location of your generators, whether they’re on-site, in transit, or stored in a warehouse. This capability allows you to respond quickly to customer needs and optimize logistics.
This level of visibility is especially essential when dealing with time-sensitive equipment like generators, where downtime can lead to significant losses. By knowing exactly where your generators are, you can dispatch technicians more efficiently, reduce travel time, and ensure that the right parts are sent to the right location.
Real-time location tracking also helps you manage your inventory more effectively. You can see which generators are available, which ones are in use, and which ones need maintenance or repairs.
This information enables you to make informed decisions about resource allocation, ensuring that you have the right equipment in the right place at the right time. With real-time location tracking, you can streamline your operations, improve customer satisfaction, and increase revenue.
Asset Performance Analytics
By analyzing equipment performance data, you can identify trends and patterns that help pinpoint potential issues before they become major problems. This allows you to take proactive measures to prevent downtime and guarantee your generators are always running at peak levels.
With asset performance analytics, you can:
-
Monitor equipment performance in real-time, allowing you to quickly respond to anomalies and deviations.
-
Identify areas of inefficiency and opportunities for improvement.
-
Enhance maintenance schedules based on actual equipment usage and condition.
-
Reduce energy consumption and lower operating costs.
-
Improve overall reliability and extend the lifespan of your equipment.
Maximizing Resource Allocation
You can optimize resource allocation by allocating personnel, materials, and equipment to maintenance tasks based on real-time data and priority, guaranteeing that your team is working efficiently and effectively to minimize downtime. This means you can assign the right technician to the right job, with the right tools and materials, at the right time.
With equipment tracking software, you’ll have a clear view of your resources and can make informed decisions about how to allocate them.
You’ll also be able to identify areas where resources are being wasted or underutilized, and make adjustments accordingly. For example, if you notice that a particular technician is consistently finishing jobs ahead of schedule, you can reassign them to more pressing tasks.
Similarly, if you see that a certain type of equipment is frequently in high demand, you can guarantee that you have an adequate supply on hand.
Data-Driven Business Decisions
Generator maintenance teams leveraging equipment tracking software can tap into a wealth of data to inform their business decisions.
You’ll have access to valuable insights that help you identify areas of improvement, optimize operations, and drive growth. With equipment tracking software, you can make data-driven decisions that reduce costs, increase efficiency, and enhance customer satisfaction.
Some key benefits of data-driven decision-making for your generator maintenance business include:
-
Identifying trends and patterns: Analyze equipment performance and maintenance data to identify trends and patterns that inform your maintenance strategies.
-
Optimizing resource allocation: Use data to determine the most efficient ways to allocate resources, such as personnel and equipment.
-
Improving customer satisfaction: Leverage data to identify areas where you can improve customer satisfaction, such as reducing response times or increasing first-time fix rates.
-
Reducing costs: Analyze data to identify opportunities to reduce costs, such as minimizing fuel consumption or extending equipment lifecycles.
-
Driving business growth: Use data to identify new business opportunities, such as upselling or cross-selling services to existing customers.
Frequently Asked Questions
Can Equipment Tracking Software Integrate With Our Existing Field Service Management System?
You’re wondering if the new software can sync with your existing system, right? Yes, you can integrate equipment tracking software with your current field service management system, allowing seamless data flow and reduced manual errors.
Is Equipment Tracking Software Compatible With Various Device Types and Operating Systems?
You’ll be glad to know that most equipment tracking software is designed to be compatible with various device types and operating systems, allowing you to access and track your equipment seamlessly across different platforms.
How Does Equipment Tracking Software Handle Equipment That Is Rented or Leased?
When you’re dealing with rented or leased equipment, you’ll want software that can track ownership and usage separately, allowing you to monitor and manage assets without worrying about who owns them.
Can Equipment Tracking Software Be Customized to Meet Our Specific Business Needs?
You’ll find that most software solutions can be tailored to fit your unique needs. You can customize fields, workflows, and reports to mirror your business processes, ensuring a seamless integration that boosts efficiency and productivity.
What Kind of Customer Support Does the Equipment Tracking Software Provider Offer?
When evaluating a software provider, you’ll want to know what kind of customer support they offer. Do they provide 24/7 assistance, online resources, and regular updates? You’ll need a team that’s responsive to your needs and helps you troubleshoot issues quickly.
Conclusion
By implementing equipment tracking software, you’ll be able to streamline your generator maintenance field service business, reduce downtime, and boost revenue potential.
With real-time visibility into equipment location, status, and maintenance history, you’ll make data-driven decisions, optimize resource allocation, and enhance customer satisfaction.
By automating maintenance scheduling, tracking location, and analyzing asset performance, you’ll take your business to the next level and stay ahead of the competition.
Disclaimer: Some information is provided through AI. Users should always conduct their own research and consult with qualified professionals before making any decisions.Affiliate information declaration: We may earn revenue from the products referred on this page and participate in affiliate programs.Related Posts

Try Now
ServiceFolder's field service scheduling software free plan is perfect for small businesses with up to three people or less. It includes time tracking, scheduling, and mobile app features that make it one of the best mobile field service management software solutions for small businesses available. It is perfect for any small business company within the field service industry that wants to use technology to increase performance and productivity.