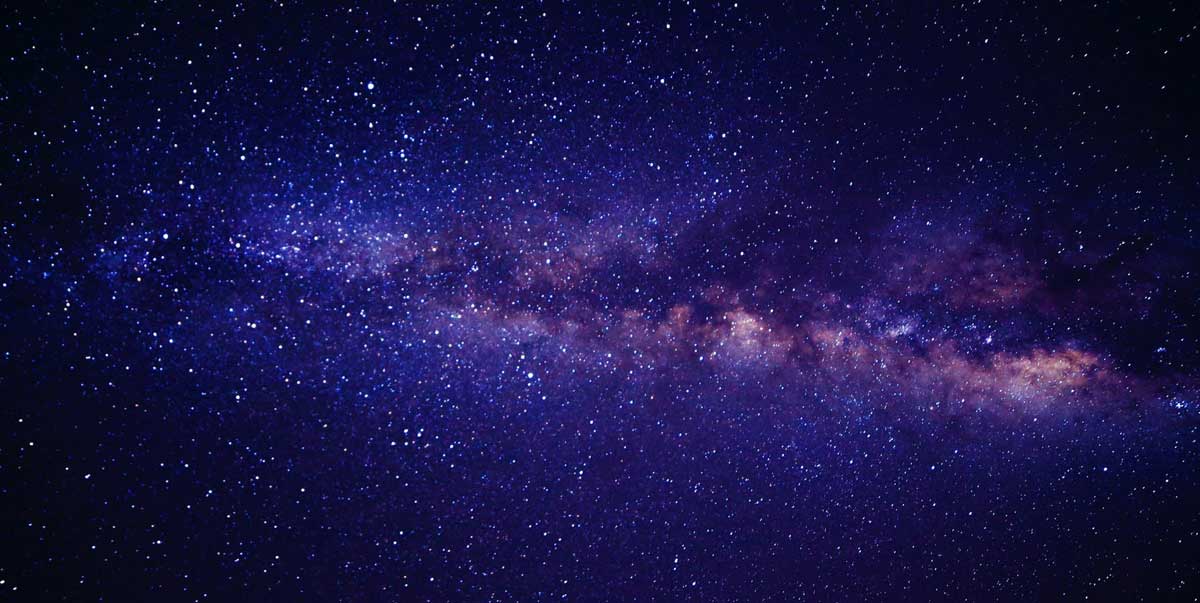
Why Predictive Maintenance Is Important
Are you tired of unexpected breakdowns and costly repairs? Do you want to maximize the lifespan of your equipment while minimizing downtime? If so, then predictive maintenance is the solution you’ve been looking for. In this article, we will explore why predictive maintenance is important and how it can revolutionize your maintenance routine.
Predictive maintenance involves using data and advanced analytics to predict when machinery or equipment is likely to fail. By analyzing factors such as temperature, vibration patterns, and usage history, predictive maintenance systems can identify potential issues before they become major problems. This proactive approach allows you to schedule repairs or replacements at a time that is convenient for your operations, reducing unplanned downtime and improving overall productivity. With predictive maintenance, you no longer have to wait for something to break down before taking action - instead, you can stay one step ahead by addressing issues before they escalate. So why wait until it’s too late? Embrace the power of predictive maintenance and experience the benefits for yourself.
ServiceFolder's Field Service Management Software provides complete software solutions for back office and field service technicians for the Equipment Maintenance Businesses.
What is Predictive Maintenance?
If you want to understand the significance of predictive maintenance, you need to know that it’s all about using advanced analytics and machine learning algorithms to predict when equipment is likely to fail. This article section aims to explain what predictive maintenance is and why it is important. Predictive maintenance involves analyzing historical data, real-time sensor readings, and other relevant information to identify patterns or anomalies that could indicate potential failures in machinery or equipment. By doing so, organizations can proactively schedule maintenance activities before a breakdown occurs, avoiding costly unplanned downtime and reducing repair costs. Implementing predictive maintenance strategies can also optimize asset lifespan, improve overall operational efficiency, and enhance safety by preventing accidents caused by faulty equipment. In conclusion, understanding what predictive maintenance entails is crucial as it plays a vital role in ensuring the smooth operation of industrial processes while minimizing disruptions and maximizing productivity.
Advantages and Disadvantages
When considering the advantages and disadvantages of predictive maintenance, you will find that it can greatly streamline operations and improve efficiency. Here are four reasons why predictive maintenance is important:
-
Cost savings: By using predictive maintenance techniques, you can identify potential issues before they become major problems. This proactive approach allows for timely repairs or replacements, reducing downtime and minimizing costly emergency repairs.
-
Increased equipment lifespan: Regular maintenance based on data-driven insights helps to extend the lifespan of your assets. By detecting early signs of wear and tear, you can take preventive measures to ensure optimal performance and avoid premature failures.
-
Improved safety: Predictive maintenance enables better planning and scheduling of maintenance activities, reducing the risk of accidents or injuries caused by unexpected equipment failures. It also ensures that all safety protocols are followed during routine inspections and repairs.
-
Enhanced asset management: With real-time monitoring and analysis of data, predictive maintenance provides valuable information about asset health, usage patterns, and performance trends. This allows for better decision-making regarding repair versus replacement, optimizing resource allocation, and improving overall asset management strategies.
Predictive maintenance offers numerous advantages such as cost savings, increased equipment lifespan, improved safety measures, and enhanced asset management capabilities. By implementing this proactive maintenance solution in your operations, you can optimize efficiency while minimizing downtime and costs associated with unplanned breakdowns or failures.
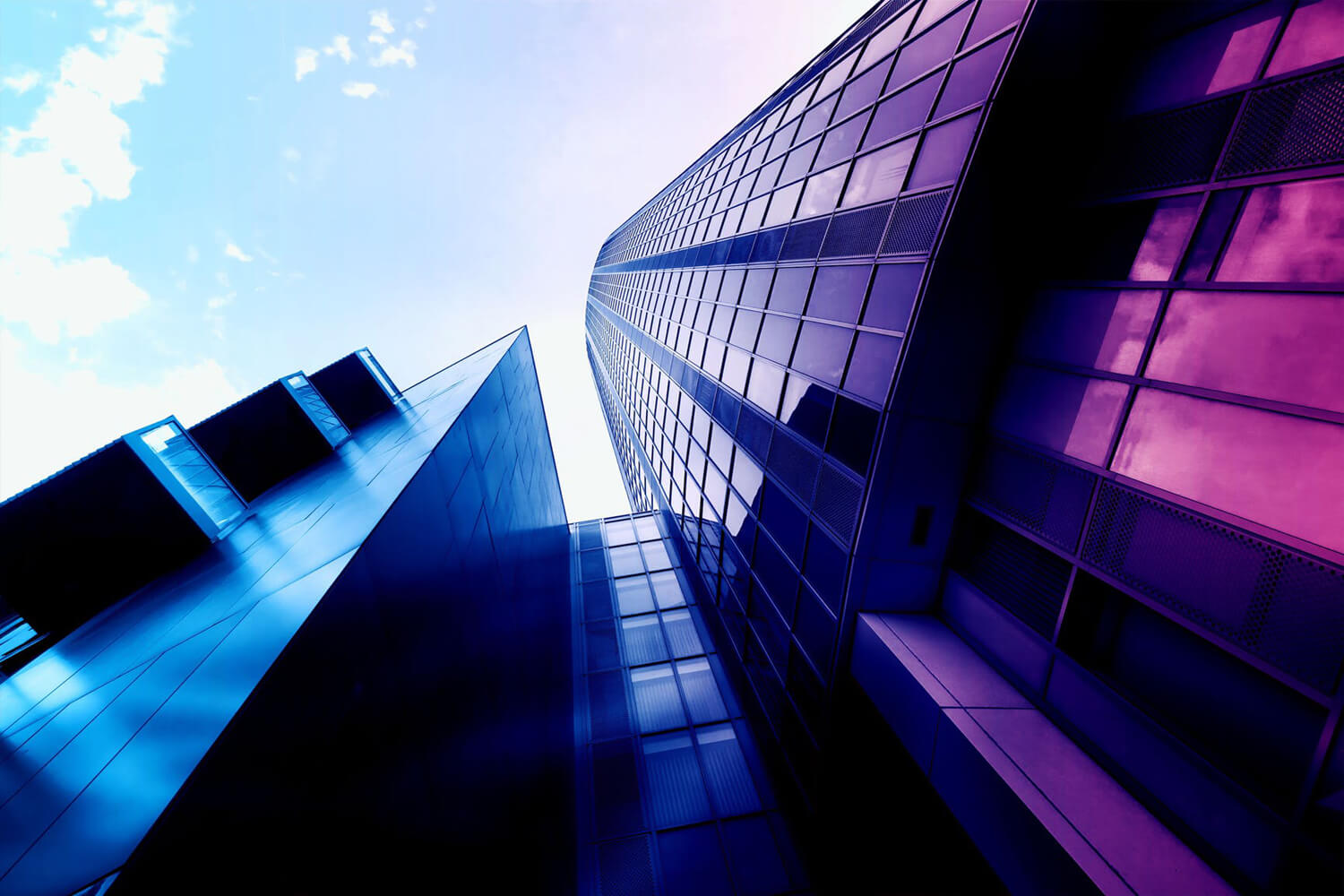
Discover more ServiceFolder Features for your
Equipment Maintenance Businesses
Contact Us
Free - 1 User
Benefits of Predictive Maintenance
You’ll be amazed at the incredible perks you’ll reap from implementing this cutting-edge proactive maintenance solution in your operations. Predictive maintenance offers numerous benefits that can greatly enhance your business. By using advanced analytics and machine learning algorithms, you can accurately predict when equipment is likely to fail, allowing you to schedule maintenance activities more efficiently and avoid costly unplanned downtime. This not only saves you money on repairs but also improves the overall efficiency of your operations. With predictive maintenance, you can identify potential issues before they become major problems, resulting in increased equipment uptime and productivity. Additionally, by addressing maintenance needs proactively, you can extend the lifespan of your equipment and reduce the need for frequent replacements or repairs. Overall, predictive maintenance is a game-changer when it comes to optimizing cost-effectiveness and operational efficiency in your organization.
Implementing a Predictive Maintenance Routine
By incorporating advanced analytics and machine learning, you can accurately anticipate equipment failures, optimize maintenance schedules, and increase operational efficiency. Implementing a predictive maintenance routine is essential for businesses to ensure the reliability and longevity of their assets. By regularly monitoring the health of equipment using data-driven insights, you can identify potential issues before they escalate into major failures. This proactive approach allows you to plan maintenance activities in advance, minimizing downtime and reducing costs associated with unexpected breakdowns. Additionally, a well-implemented predictive maintenance strategy enables you to optimize your maintenance resources by performing tasks only when necessary based on actual equipment conditions. This not only saves time but also reduces unnecessary expenses on preventative or corrective maintenance that may not be required. Overall, implementing a predictive maintenance routine empowers businesses to maximize the lifespan of their assets while improving operational efficiency and reducing costs.
Get started with ServiceFolder
- Manage Jobs & Staff
- On Site Quote and Invoice
- On Site Notes and Photos
- Sync with Quickbooks Online
- Print Designer for all Documents
- Equipment/Asset Management
- Customer Management
- Leads Management
- Inventory Management
- Customer Notifications
- Customer Fields
- PriceBooks
How Predictive Maintenance Works
Implementing advanced analytics and machine learning allows you to accurately predict equipment failures, optimizing your maintenance schedules and increasing operational efficiency to extraordinary levels. With a predictive maintenance program in place, you can avoid unexpected breakdowns and minimize downtime by continuously monitoring the condition of your equipment. By utilizing various sensors and data collection techniques, you can gather real-time information about the performance and health of your assets. This data is then analyzed using sophisticated algorithms that identify patterns and anomalies, allowing you to anticipate potential issues before they occur. By proactively addressing maintenance needs based on these predictions, you can prevent costly breakdowns, reduce unplanned downtime, and extend the lifespan of your equipment. The following table provides an overview of how predictive maintenance works:
Step | Description |
---|---|
1 | Data Collection: Collect relevant data from sensors and other sources about the performance and condition of equipment. |
2 | Data Analysis: Use advanced analytics and machine learning algorithms to analyze the collected data for patterns or anomalies. |
3 | Prediction: Predict potential failures or performance degradation based on the analysis results. |
4 | Action: Take proactive measures such as scheduling preventive maintenance or repairing identified issues before they cause major problems. |
By implementing a comprehensive predictive maintenance program that incorporates condition monitoring techniques, you can significantly improve the reliability of your assets while reducing costs associated with reactive repairs or replacements.
Leveraging Predictive Maintenance Technology
Now that you understand how predictive maintenance works, let’s dive into the next article section and explore how to leverage predictive maintenance technology. This is where things get really exciting! By utilizing advanced technologies like artificial intelligence, machine learning, and data analytics, predictive maintenance can revolutionize your maintenance strategy. These cutting-edge tools allow you to gather real-time data from various sensors and equipment, identify patterns and anomalies, and predict when a failure is likely to occur. By leveraging this technology effectively, you can optimize your maintenance schedules, reduce downtime, extend the lifespan of your assets, and ultimately save costs. It’s clear that embracing predictive maintenance technology is not just important but essential in today’s fast-paced industrial landscape.
Try all in one Equipment Maintenance Businesses Software - Free - 1 UserPredictive vs. Preventive Maintenance
Utilizing cutting-edge technology such as artificial intelligence and machine learning, you can discern the distinction between predictive and preventive maintenance. Predictive maintenance involves analyzing real-time data to predict when equipment is likely to fail, allowing for proactive repairs or replacements. On the other hand, preventive maintenance follows a scheduled approach, where regular inspections and servicing are conducted to prevent breakdowns. The comparison between predictive and preventive maintenance highlights the importance of adopting a predictive approach. By predicting failures before they occur, businesses can avoid unexpected downtime, reduce repair costs, and optimize their operational efficiency. This article section emphasizes the significance of leveraging predictive maintenance technology in order to stay ahead in today’s competitive landscape.
The Impact of Predictive Maintenance
Maximizing the efficiency and longevity of your equipment is like having a crystal ball that reveals hidden insights into its future, allowing you to foresee potential issues before they transform into costly disasters. Predictive maintenance has a significant impact on maintenance costs and downtime, providing numerous benefits for businesses. By utilizing advanced technologies and data analysis, predictive maintenance enables you to detect early signs of equipment failure and schedule maintenance activities accordingly. This proactive approach helps minimize unplanned downtime, reducing the risk of production interruptions and associated financial losses. Additionally, by identifying potential problems in advance, predictive maintenance allows you to plan repairs more effectively, optimizing the allocation of resources and minimizing overall maintenance costs. The following table illustrates some key advantages of implementing predictive maintenance:
Benefits | Description |
---|---|
Increased Equipment Life | Early detection of issues allows for timely repairs or replacements, prolonging the lifespan of critical assets. |
Cost Savings | Proactively addressing equipment failures reduces repair expenses while avoiding costly emergency repairs and production loss. |
Improved Efficiency | Regular monitoring and analysis optimize equipment performance, leading to increased productivity and reduced energy consumption. |
Enhanced Safety | Identifying potential safety hazards in advance ensures prompt actions are taken to prevent accidents or injuries. |
Data-Driven Decision Making | Leveraging data analytics enables informed decision making regarding asset management strategies and resource allocation. |
Predictive maintenance plays a crucial role in minimizing downtime, reducing costs, extending equipment life, improving efficiency, enhancing safety measures, and facilitating data-driven decision making within organizations. Embracing this proactive approach can help businesses gain a competitive edge by maximizing their operational effectiveness while staying ahead of potential setbacks.
Empowering Your Maintenance Team
By empowering your maintenance team, you can unlock their full potential and tap into their expertise to optimize equipment performance and ensure smooth operations. Here are three ways in which empowering your maintenance team is important in the context of predictive maintenance:
-
Increased Efficiency: When you empower your maintenance team, they feel more confident and motivated to take ownership of their work. This leads to increased efficiency as they become more proactive in identifying and resolving potential issues before they escalate. By giving them the necessary tools, training, and authority, you enable them to make informed decisions that ultimately improve equipment reliability and reduce downtime.
-
Enhanced Collaboration: Empowering your maintenance team fosters a culture of collaboration where they feel comfortable sharing their insights and ideas. This encourages knowledge sharing among team members, enabling them to learn from each other’s experiences and find innovative solutions together. By leveraging the collective expertise of your maintenance team, you can identify patterns or trends that may go unnoticed otherwise, leading to more accurate predictions and better preventive measures.
-
Continuous Improvement: Empowered maintenance teams are not afraid to challenge the status quo or suggest improvements in existing processes or procedures. They have a deep understanding of the equipment they maintain on a daily basis and can provide valuable feedback for optimizing its performance. By creating an environment that encourages continuous improvement, you foster innovation within your maintenance team, allowing them to adapt quickly to changing technologies or requirements.
Empowering your maintenance team is crucial in the realm of predictive maintenance because it increases efficiency, enhances collaboration, and promotes continuous improvement. By recognizing the importance of their expertise and providing them with the necessary resources and support, you can harness their full potential to ensure optimal equipment performance and overall operational success.
Tips for a Preventive Maintenance Plan
Now that you understand the importance of empowering your maintenance team, let’s delve into the tips for creating a preventive maintenance plan. As a facility manager, it is crucial to implement a proactive approach to maintenance by developing a well-structured preventive maintenance plan. This plan focuses on conducting regular inspections and servicing equipment before any failures occur. By integrating predictive maintenance techniques into your plan, you can identify potential issues before they escalate and cause significant disruptions or costly repairs. Predictive maintenance utilizes advanced analytics and data-driven insights to forecast when equipment might fail, allowing you to schedule maintenance at optimal times. The benefits of predictive maintenance are numerous - it reduces unplanned downtime, extends the lifespan of assets, increases operational efficiency, decreases repair costs, and enhances overall productivity. Implementing an effective preventive maintenance plan with elements of predictive maintenance will ultimately lead to improved reliability and performance within your facility.
When is Predictive Maintenance Suitable?
Timing is everything when it comes to implementing a proactive maintenance strategy, and knowing when the perfect moment arises to embrace predictive maintenance can be the key to unlocking unparalleled efficiency and cost savings. Predictive maintenance is suitable in various scenarios where it can provide significant benefits. Here are three factors to consider:
-
Equipment criticality: Predictive maintenance is particularly beneficial for equipment that plays a crucial role in the production process or has a high impact on operations. By continuously monitoring such equipment, potential failures can be detected early on, preventing costly breakdowns and reducing downtime.
-
Data availability: Implementing predictive maintenance requires access to relevant data from the equipment being monitored. This includes data such as temperature, vibration levels, or oil analysis results. Without this data, it becomes challenging to accurately predict potential failures.
-
Maintenance costs: Another factor to consider is the cost of preventive or reactive maintenance compared to predictive maintenance. If preventive or reactive approaches result in high expenses due to frequent repairs or unnecessary preventive actions, switching to predictive maintenance can lead to significant cost savings over time.
Considering these factors will help determine if and when predictive maintenance is suitable for your organization’s specific needs. Embracing this proactive approach can ultimately contribute to improved operational efficiency and reduced costs, making it an important aspect of any maintenance strategy.
Societal and Business Perspectives
Consider how embracing a proactive approach to maintenance can revolutionize both your business and society as a whole. From a societal perspective, predictive maintenance plays a crucial role in reducing downtime and improving overall efficiency. By anticipating and addressing equipment failures before they occur, businesses can minimize disruptions to essential services, such as transportation or energy supply, ensuring the smooth functioning of our daily lives. Additionally, predictive maintenance helps in preventing accidents and environmental damage by identifying potential hazards early on. From a business standpoint, implementing predictive maintenance strategies can lead to significant cost savings. By avoiding unexpected breakdowns and costly repairs, companies can optimize their resources and improve productivity. Furthermore, it enables businesses to transition from reactive models of maintenance to more strategic approaches that prioritize long-term sustainability and competitiveness. Therefore, recognizing the importance of predictive maintenance from both societal and business perspectives is key to driving positive change in our increasingly interconnected world.
Frequently Asked Questions
Can predictive maintenance be applied to any type of equipment or machinery?
Yes, predictive maintenance can be applied to any type of equipment or machinery. It uses data and analytics to forecast when maintenance is needed, helping you avoid costly breakdowns and optimize machine performance.
What are the key indicators or factors that determine when a piece of equipment will require maintenance?
While you may think it’s challenging to determine when equipment needs maintenance, there are key indicators and factors that can help. By analyzing data like performance trends and sensor readings, you can predict maintenance needs accurately.
How does predictive maintenance help in reducing downtime and increasing productivity?
Predictive maintenance helps reduce downtime and increase productivity by using data to anticipate when equipment will require maintenance. This allows for scheduled repairs, preventing unexpected breakdowns and maximizing operational efficiency.
What are some common challenges or barriers in implementing a predictive maintenance routine?
Implementing a predictive maintenance routine can be as challenging as untangling a knot. From lack of data integration to resistance from employees, these barriers require careful planning and collaboration to overcome.
How does predictive maintenance contribute to cost savings and return on investment for businesses?
Predictive maintenance helps businesses save costs and increase return on investment. By identifying potential equipment failures in advance, it allows for proactive repairs and reduces downtime. This leads to improved efficiency, productivity, and ultimately financial savings.
Conclusion
In conclusion, predictive maintenance is a game-changer for businesses and society as a whole. By harnessing the power of data and analytics, you can stay one step ahead of equipment failures, saving time, money, and resources. With predictive maintenance, you can prevent disruptions to your operations and ensure maximum uptime.
Imagine a world where machines never break down unexpectedly - that’s the kind of future that predictive maintenance offers. By implementing this proactive approach to maintenance, you can avoid costly repairs and keep your business running smoothly. It’s like having a crystal ball that predicts when something might go wrong before it even happens.
So why wait for something to break when you can prevent it from happening in the first place? Embrace the power of predictive maintenance and take control of your assets. Don’t be left in the dust while your competitors soar ahead with optimized operations. Start implementing a predictive maintenance routine today and reap the benefits tomorrow.
After all, an ounce of prevention is worth a pound of cure!
Disclaimer: Some information is provided through AI. Users should always conduct their own research and consult with qualified professionals before making any decisions.Related Posts

Try Now
ServiceFolder's field service scheduling software free plan is perfect for small businesses with up to three people or less. It includes time tracking, scheduling, and mobile app features that make it one of the best mobile field service management software solutions for small businesses available. It is perfect for any small business company within the field service industry that wants to use technology to increase performance and productivity.