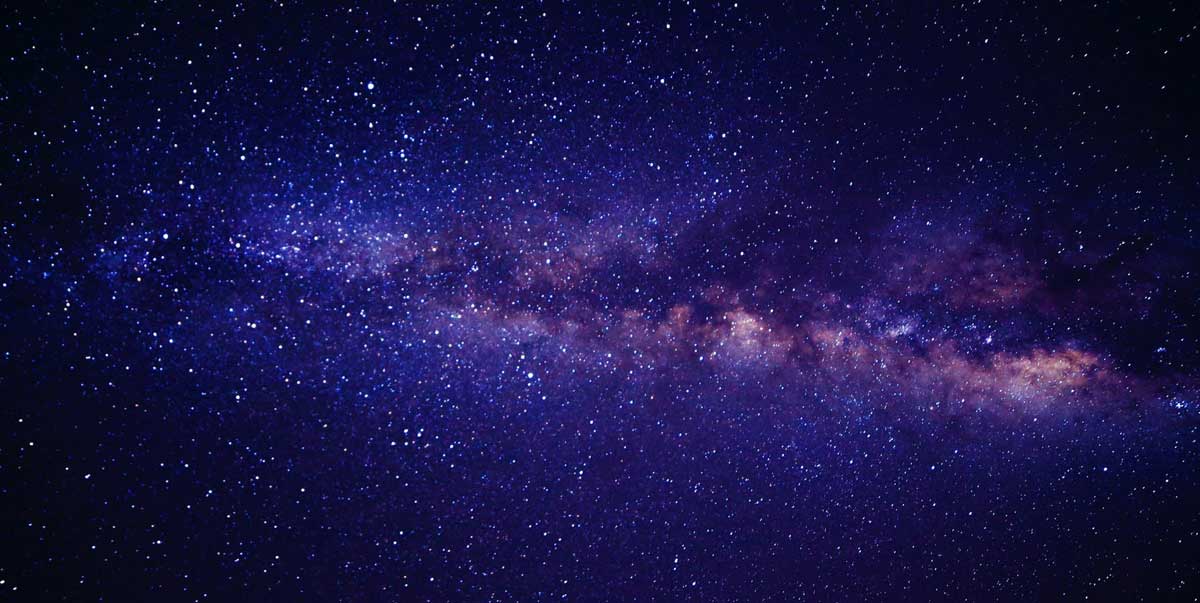
Preventive Maintenance Spare Parts
Are you tired of dealing with unexpected breakdowns and costly repairs? Do you want to increase the lifespan of your equipment and minimize downtime? Well, look no further than preventive maintenance spare parts. In this article, we will explore the importance of maintaining a stock of spare parts for your machinery and how it can benefit your business.
When it comes to managing inventory costs, preventive maintenance spare parts play a crucial role. By having a stock of commonly used spare parts readily available, you can avoid lengthy lead times and expensive rush shipping fees. This not only helps to reduce downtime but also allows you to plan and budget for maintenance tasks more effectively. With preventive maintenance spare parts on hand, you can quickly address any issues that arise, ensuring optimal functioning of your equipment and preventing small problems from turning into major headaches. So, let’s dive deeper into the world of preventive maintenance spare parts and discover how they can revolutionize your maintenance practices.
ServiceFolder's Field Service Management Software provides complete software solutions for back office and field service technicians for the Equipment Maintenance Businesses.
Managing Inventory Costs
You can save a significant amount of money by properly managing your inventory costs, like uncovering hidden gems in a thrift store that turn out to be valuable treasures. When it comes to preventive maintenance, having an efficient spare parts inventory is crucial for minimizing downtime and ensuring smooth operations. However, maintaining a large inventory can lead to unnecessary costs if not managed effectively. By implementing strategies such as forecasting demand, regularly auditing stock levels, and optimizing reorder points, you can prevent overstocking or understocking situations. This proactive approach allows you to identify potential issues before they arise and ensure that the right spare parts are readily available when needed. Additionally, collaborating closely with suppliers can help negotiate better pricing terms or explore alternative options for cost savings. Overall, managing your inventory costs is essential for maximizing efficiency and reducing expenses in your preventive maintenance processes.
Maintaining Spare Parts Stock
Imagine having a well-stocked inventory that ensures you never run into unexpected disruptions due to insufficient supplies. When it comes to preventive maintenance, maintaining a sufficient spare parts stock is crucial. By having the right spare parts readily available, you can minimize downtime and quickly address any equipment failures or breakdowns. To make it easier to manage your spare parts stock, consider using a table like the one below:
Part Name | Quantity | Manufacturer |
---|---|---|
Belt | 10 | ABC Company |
Filter | 20 | XYZ Corporation |
Valve | 5 | 123 Industries |
Motor | 8 | DEF Enterprises |
Bearing | 15 | LMN Limited |
This allows you to easily track the quantity of each part and their respective manufacturers. By regularly monitoring this table, you can identify when certain parts are running low and proactively order replacements. With a well-maintained spare parts stock, you can ensure smooth operations and reduce the risk of unexpected disruptions in your preventive maintenance routine.
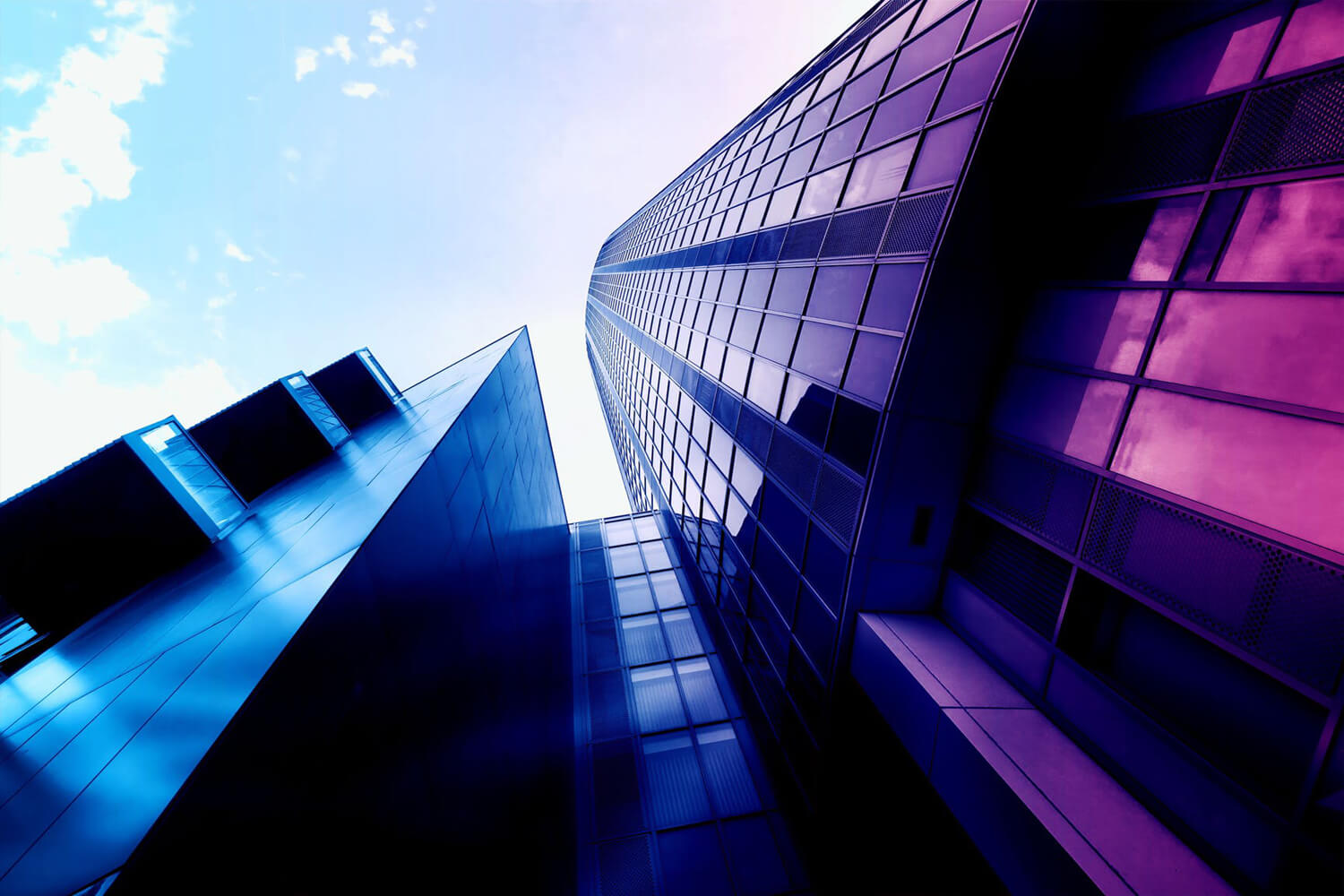
Discover more ServiceFolder Features for your
Equipment Maintenance Businesses
Contact Us
Free - 1 User
Benefits of Maintenance Software
If you’re tired of the hassle of manually tracking and managing your equipment inventory, maintenance software can provide a streamlined solution that saves you time and effort. With preventive maintenance in mind, maintenance software offers features specifically designed for spare parts management. By utilizing this software, you can easily keep track of your spare parts inventory, ensuring that you have the necessary items on hand when needed. The software allows you to set up alerts for low stock levels or upcoming maintenance tasks, so you never run out of critical spare parts again. Additionally, maintenance software provides detailed reports and analytics, giving you insights into your spare parts usage and helping you identify trends or areas for improvement. Overall, implementing maintenance software in your organization can optimize your spare parts management process and contribute to a more efficient preventive maintenance strategy.
Elements of Preventive Maintenance
One key aspect of maintaining equipment longevity is the regular inspection and servicing to prevent future issues. Implementing a preventive maintenance program ensures that all necessary actions are taken in a timely manner, including the replacement of worn-out spare parts. By identifying potential problems before they occur, you can avoid costly breakdowns and downtime. Utilizing maintenance management software further enhances the effectiveness of preventive maintenance by streamlining processes and providing real-time data on equipment performance. This enables you to schedule maintenance tasks efficiently, track spare part inventory, and generate reports for analysis and decision-making. With preventive maintenance and the support of reliable spare parts and maintenance management software, you can maximize equipment lifespan and minimize disruptions to your operations.
Get started with ServiceFolder
- Manage Jobs & Staff
- On Site Quote and Invoice
- On Site Notes and Photos
- Sync with Quickbooks Online
- Print Designer for all Documents
- Equipment/Asset Management
- Customer Management
- Leads Management
- Inventory Management
- Customer Notifications
- Customer Fields
- PriceBooks
Types of Maintenance Spares
To ensure the smooth operation of your equipment, it is crucial to have a variety of backup components readily available, acting as the protective shield against unforeseen disruptions. Preventive maintenance requires having spare parts on hand to minimize downtime and keep your equipment functioning at its best. There are different types of maintenance spares that you should consider stocking up on. First, there are consumable spares, such as filters and lubricants, which need regular replacement due to wear and tear. Then, there are repairable spares like motors or pumps that can be repaired when they malfunction instead of being replaced entirely. Additionally, critical spares for essential components that are prone to failure should also be kept in stock. These include items like circuit boards or control systems that are vital for the overall functionality of your equipment. By having a range of maintenance spares available, you can proactively address any issues that arise and keep your operations running smoothly without major disruptions.
Hidden Costs of Parts Management
Don’t overlook the hidden expenses that come with managing and maintaining your equipment’s components. When it comes to preventive maintenance and spare parts, there are often hidden costs that can add up quickly. These costs include inventory carrying costs, which encompass storage, insurance, and depreciation of spare parts. Additionally, there may be costs associated with obsolescence or spoilage of unused spare parts over time. Another hidden cost is the expense of managing and tracking spare parts, including labor costs for inventory management systems or software. It is essential to consider these hidden costs when budgeting for preventive maintenance and spare parts management to ensure overall cost-effectiveness and efficient operations.
Try all in one Equipment Maintenance Businesses Software - Free - 1 UserImproving Spare Parts Management
In order to streamline operations and cut costs, it’s crucial for businesses to enhance their inventory management of components. By improving preventive maintenance spare parts management, companies can optimize their processes and increase efficiency. Here are three key ways to achieve this:
- Implement a centralized inventory system: Having a centralized database or software that tracks all spare parts can help businesses keep track of their stock levels, identify when reordering is necessary, and prevent overstocking or understocking issues.
- Conduct regular audits: Regularly auditing the spare parts inventory ensures accuracy and helps identify any discrepancies or obsolete items. This allows businesses to make informed decisions on what parts need to be replenished or removed from the inventory.
- Establish strong supplier relationships: Building strong relationships with reliable suppliers is essential for timely delivery of spare parts. Maintaining open communication channels with suppliers can ensure quick response times in emergencies and reduce downtime.
By adopting these practices, companies can effectively improve their preventive maintenance spare parts management, leading to cost savings and smoother operations.
Using CMMS for Maintenance
Managing maintenance tasks becomes easier and more efficient when using a CMMS system. With a CMMS, you can easily keep track of your parts inventory and ensure that you have the necessary spare parts available when needed. The software allows for efficient parts management by providing real-time updates on inventory levels, automating reordering processes, and tracking usage patterns. By having an accurate and up-to-date record of your parts inventory, you can avoid unnecessary downtime caused by lacking essential spare parts. Additionally, CMMS systems provide valuable insights into maintenance trends and help optimize your spare parts management strategy. Overall, implementing a CMMS system can streamline your maintenance operations and improve overall efficiency in managing preventive maintenance spare parts.
Issues with Spare Parts Management
One major challenge in effectively managing spare parts is the lack of accurate inventory tracking, which can lead to costly delays and disruptions in maintenance operations. To address this issue, it is crucial to have a reliable computerized maintenance management system (CMMS) that can accurately track spare parts inventory levels. This allows for timely reordering and replenishment of critical components, reducing the risk of unexpected downtime. Additionally, implementing barcode or RFID technology can enhance inventory accuracy by automating data collection and minimizing human error. Another important aspect of spare parts management is proper storage and organization. Creating a well-structured storage system with labeled bins or shelves ensures easy identification and retrieval of required parts when needed. Regular audits should also be conducted to identify obsolete or excess inventory that can be disposed of or repurposed. By addressing these issues with spare parts management, preventive maintenance programs can operate smoothly, minimizing equipment downtime and optimizing operational efficiency.
Standardization in Parts Management
Now that you understand the issues with spare parts management, let’s dive into the importance of standardization in parts management for preventive maintenance. When it comes to maintaining equipment and machinery, having a standardized approach to spare parts is crucial. Standardization in parts management ensures that the right spare parts are readily available when needed for preventive maintenance tasks. By establishing a standardized system, you can streamline the process of identifying, sourcing, and storing spare parts, reducing downtime and increasing efficiency. Additionally, standardization enables better inventory control and cost management by eliminating duplicate or unnecessary parts. With an organized and standardized approach to spare parts management, you can optimize your preventive maintenance efforts and keep your equipment operating at its best.
Frequently Asked Questions
How can preventive maintenance spare parts contribute to overall cost savings in the long run?
By using preventive maintenance spare parts, you can save costs in the long run. Regularly replacing worn-out components before they cause major breakdowns can prevent costly repairs and downtime.
What are some common challenges faced in managing spare parts inventory?
Managing spare parts inventory can be challenging. Some common issues include inaccurate forecasting, overstocking or understocking, lack of visibility, and difficulty in tracking and organizing the inventory.
Is it possible to track the usage and lifespan of spare parts using maintenance software?
Yes, you can track the usage and lifespan of spare parts using maintenance software. Imagine being able to see that a particular part has been used 100 times, providing valuable insights for future replacements.
What are the key factors to consider when selecting preventive maintenance spare parts?
When selecting spare parts for preventive maintenance, consider factors such as compatibility with existing equipment, reliability of the supplier, cost-effectiveness, availability, and quality. These factors will ensure efficient and effective maintenance operations.
How can the implementation of a Computerized Maintenance Management System (CMMS) improve spare parts management efficiency?
By implementing a computerized maintenance management system (CMMS), you can greatly enhance the efficiency of spare parts management. It allows for streamlined tracking, inventory optimization, and timely reordering, resulting in reduced downtime and cost savings.
Disclaimer: Some information is provided through AI. Users should always conduct their own research and consult with qualified professionals before making any decisions.Related Posts

Try Now
ServiceFolder's field service scheduling software free plan is perfect for small businesses with up to three people or less. It includes time tracking, scheduling, and mobile app features that make it one of the best mobile field service management software solutions for small businesses available. It is perfect for any small business company within the field service industry that wants to use technology to increase performance and productivity.