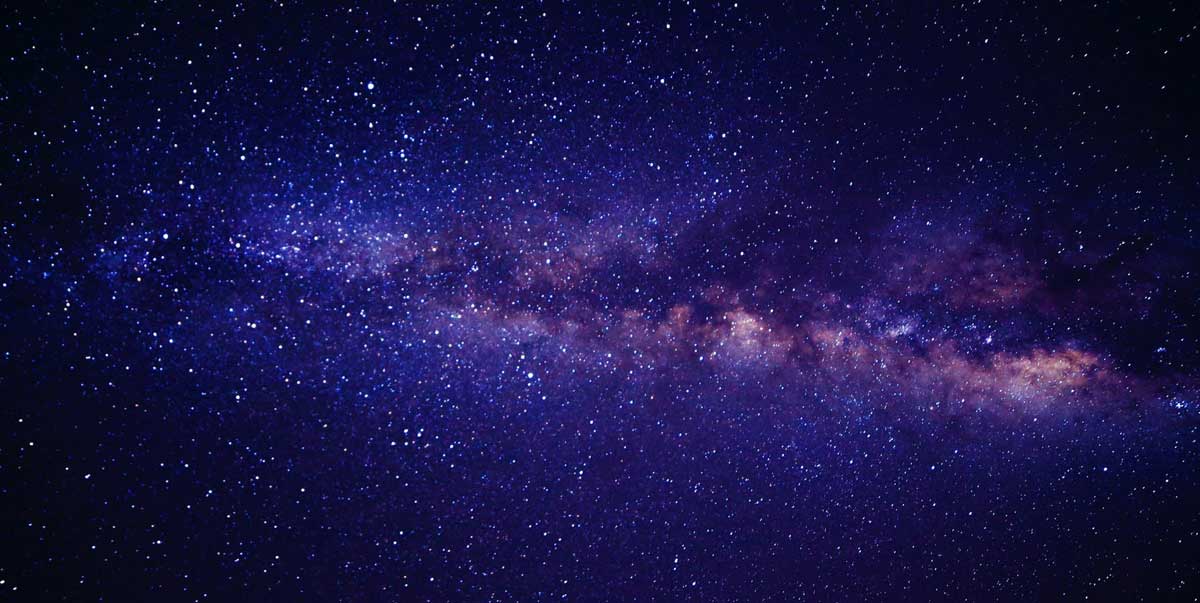
Lean Manufacturing Guide
Are you looking to optimize your manufacturing processes and increase efficiency? Look no further! In this comprehensive guide, we will provide you with all the tools and techniques you need to implement lean manufacturing principles in your operations. Lean manufacturing is a systematic approach that focuses on eliminating waste, streamlining workflow, and continuously improving processes. By following the strategies outlined in this guide, you can transform your operations into a highly efficient and cost-effective system.
In the first paragraph of this article, we will introduce the concept of lean manufacturing and explain its benefits. We will highlight how it can help businesses reduce costs, improve quality, and enhance customer satisfaction. The second paragraph will give readers an overview of what they can expect from the guide. We will mention some of the key topics covered such as identifying waste, implementing just-in-time inventory management, utilizing value stream mapping techniques, and measuring key performance indicators. By setting clear expectations in the introduction, readers will be motivated to continue reading and learn more about how lean manufacturing can benefit their operations.
ServiceFolder's Field Service Management Software provides complete software solutions for back office and field service technicians for the Equipment Maintenance Businesses.
Understanding the Principles of Lean Manufacturing
So, you want to know what makes lean manufacturing so special? Well, let’s dive into the principles that make it a game-changer. Lean manufacturing is all about continuous improvement, standardized work, and eliminating waste. By focusing on continuous improvement, you are constantly striving to find better ways of doing things and making incremental changes to optimize efficiency. Standardized work ensures that everyone follows the same processes and procedures, reducing variability and increasing quality. And perhaps most importantly, lean manufacturing aims to eliminate waste in all its forms - whether it be wasted time, materials, or resources. By streamlining operations and getting rid of unnecessary steps or activities, lean manufacturing allows companies to operate more efficiently and effectively. So if you’re looking for a way to improve productivity and reduce costs, then incorporating the principles of lean manufacturing is definitely the way to go!
Identifying and Eliminating Waste in Your Operations
To identify and eliminate waste in your operations, you need to take a close look at every step of the process and cut out anything that doesn’t add value, as the saying goes, ‘A stitch in time saves nine.’ In lean manufacturing, the goal is to reduce waste in order to improve efficiency and maximize productivity. Waste can come in various forms, such as overproduction, excess inventory, unnecessary motion or transportation, defects or rework, waiting time, and even wasted talent or creativity. By identifying these areas of waste and implementing strategies to eliminate them, you can streamline your operations and achieve significant cost savings. This requires continuous monitoring and analysis of your processes to identify bottlenecks or inefficiencies that can be addressed. Additionally, involving employees at all levels in this process can lead to valuable insights and innovative solutions for reducing waste. Remember that every small improvement adds up over time and contributes to overall efficiency gains.
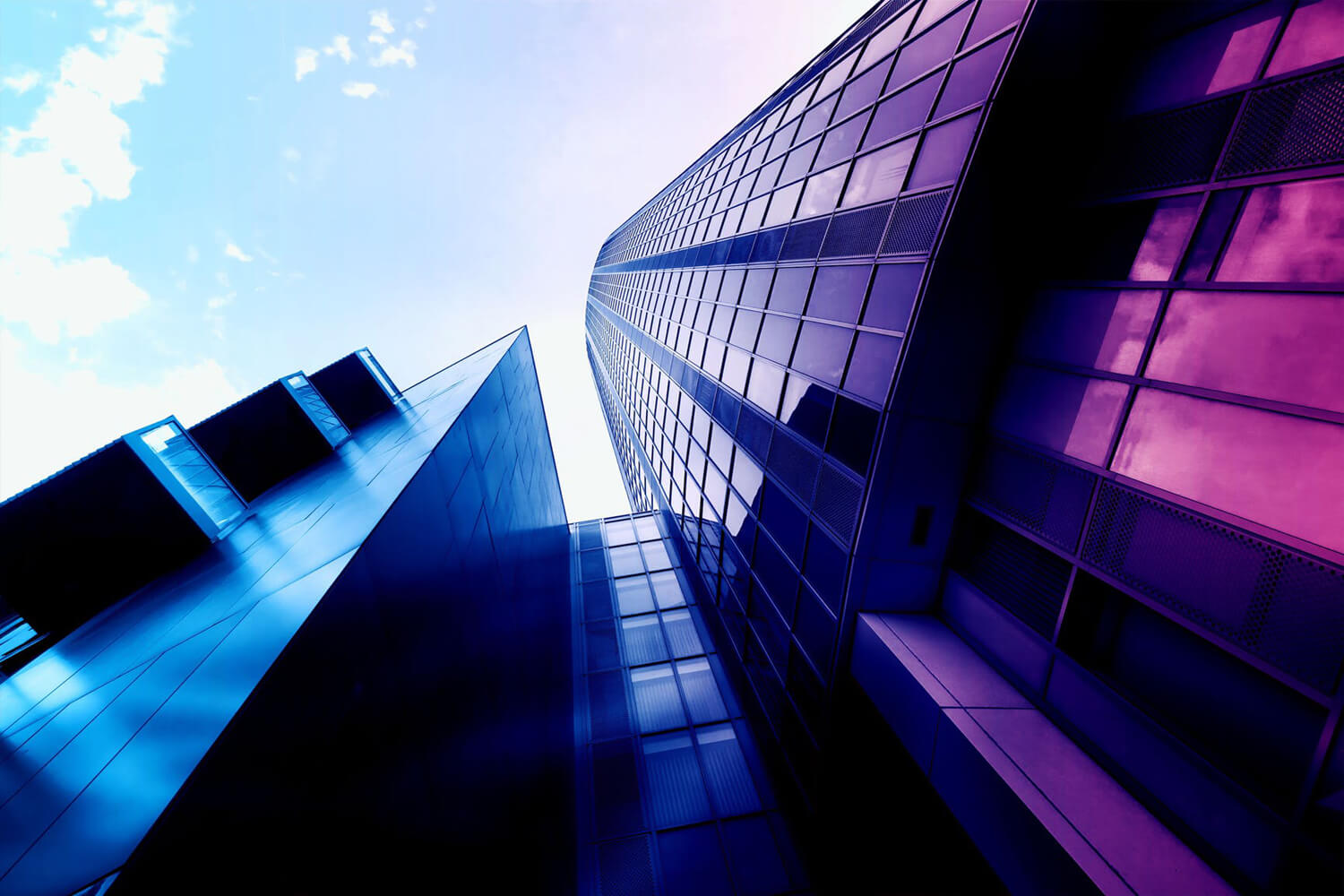
Discover more ServiceFolder Features for your
Equipment Maintenance Businesses
Contact Us
Free - 1 User
Streamlining Workflow for Increased Efficiency
By streamlining workflow, you can enhance operational efficiency and achieve greater productivity in your organization. One effective tool for achieving this is stream mapping, which is a key concept in lean manufacturing. Stream mapping allows you to visually map out the steps involved in your workflow and identify any bottlenecks or areas of waste. By analyzing this map, you can then make informed decisions on how to streamline the process and eliminate unnecessary steps or activities. This not only saves time but also reduces costs and improves overall quality. By implementing lean manufacturing principles and continuously evaluating your workflow, you can ensure that your operations are running smoothly and efficiently, leading to increased productivity in your organization.
Implementing Just-in-Time Inventory Management
Implementing just-in-time inventory management can significantly reduce storage costs and minimize waste, but how can organizations ensure they have enough inventory to meet customer demand without overstocking? Here are four strategies to help achieve this balance:
-
Accurate forecasting: By analyzing historical data and market trends, organizations can make informed predictions about future customer demand. This allows them to adjust their inventory levels accordingly, ensuring they have the right amount of stock on hand.
-
Strong supplier relationships: Building strong relationships with reliable suppliers is essential for just-in-time inventory management. Organizations should work closely with their suppliers to establish efficient communication channels and develop trust. This collaboration enables quick response times and reduces lead times, helping organizations meet unexpected spikes in customer demand.
-
Continuous improvement: Lean manufacturing principles emphasize continuous improvement in all aspects of operations, including inventory management. By regularly reviewing processes and identifying areas for improvement, organizations can streamline their supply chain and eliminate waste, ultimately enhancing their ability to meet customer demand.
-
Flexible production capabilities: Just-in-time inventory management requires a high level of flexibility in production capabilities. Organizations should invest in technology and equipment that allow for quick changeovers between different products or variations. This agility enables them to respond rapidly to changes in customer demand while maintaining minimal levels of inventory.
By implementing these strategies, organizations can effectively manage their just-in-time inventory system while meeting customer demand without unnecessary stockpiling or wastage.
Get started with ServiceFolder
- Manage Jobs & Staff
- On Site Quote and Invoice
- On Site Notes and Photos
- Sync with Quickbooks Online
- Print Designer for all Documents
- Equipment/Asset Management
- Customer Management
- Leads Management
- Inventory Management
- Customer Notifications
- Customer Fields
- PriceBooks
Applying Value Stream Mapping Techniques
Visualize your organization’s value stream and identify areas of improvement by applying value stream mapping techniques. Value stream mapping is a powerful tool used in lean manufacturing to analyze and improve the flow of materials and information throughout the entire production process. By creating a visual representation of the current state of your value stream, you can easily identify bottlenecks, waste, and inefficiencies. This allows you to prioritize areas for improvement and develop strategies to streamline operations. Through value stream mapping, you can eliminate non-value-added activities, reduce lead times, increase productivity, and ultimately enhance customer satisfaction. By applying these techniques outlined in the lean manufacturing guide, you can optimize your organization’s processes and achieve greater operational efficiency.
Engaging Employees in Continuous Improvement
Get your team on board and empower them to be active participants in the continuous improvement journey, like a conductor leading a symphony orchestra to create harmonious melodies of efficiency and innovation. Engaging employees in continuous improvement is a crucial aspect of lean manufacturing techniques. By involving your team in the process, you tap into their knowledge and expertise, fostering a sense of ownership and commitment. This not only boosts morale but also encourages collaboration and creativity, leading to better problem-solving and innovative solutions. To engage employees effectively, it is important to provide training and education on lean principles, encourage open communication channels for feedback and ideas, recognize and reward contributions, and create a culture that values continuous improvement. By doing so, you create an environment where employees feel empowered to contribute their best efforts towards achieving organizational goals while continuously striving for excellence.
Benefits | Strategies |
---|---|
Increased employee morale | Provide training on lean principles |
Enhanced problem-solving skills | Encourage open communication |
Improved collaboration & creativity | Recognize & reward contributions |
Cultivate a culture of continuous improvement | Foster an environment that values excellence |
Utilizing Kanban Systems for Visual Management
Maximize your team’s productivity and efficiency by utilizing kanban systems for visual management. With a pull system approach, kanban systems help eliminate waste and streamline workflow by focusing on the actual needs of the process. By visually representing work items and their status, it becomes easier to identify bottlenecks, prioritize tasks, and track progress in real-time. This encourages collaboration and empowers employees to take ownership of their work while fostering a culture of continuous improvement. Implementing kanban systems aligns with lean thinking principles, enabling teams to reduce lead times, increase throughput, minimize inventory levels, and enhance overall customer satisfaction.
Implementing 5S Methodology for Workplace Organization
Implementing the 5S methodology for workplace organization can greatly enhance efficiency and productivity by creating a clean and organized work environment. In lean manufacturing, it is crucial to eliminate waste and streamline processes, and the 5S methodology provides a systematic approach to achieve this. The five steps of 5S - Sort, Set in Order, Shine, Standardize, Sustain - help employees declutter their workspaces, arrange tools and materials in an efficient manner, maintain cleanliness through regular cleaning routines, establish standardized procedures, and ensure sustainability by promoting continuous improvement. By implementing the 5S methodology, companies can reduce time wasted searching for tools or information, minimize errors caused by disorganization or poor visibility of work areas, and create a culture of discipline that supports lean principles. Ultimately, workplace organization plays a vital role in optimizing workflow and improving overall operational performance.
Reducing Set-Up Time with SMED Techniques
Now that you have implemented the 5S methodology for workplace organization, it’s time to take your lean manufacturing practices a step further by focusing on reducing set-up time with SMED techniques. This technique, which stands for Single Minute Exchange of Die, is all about minimizing the amount of time it takes to change over from one production run to another. By optimizing and streamlining your set-up processes, you can significantly reduce downtime and increase productivity. Here are four compelling reasons why implementing SMED techniques is crucial for lean manufacturing success:
-
Improved Efficiency: By analyzing your current set-up procedures and eliminating non-value-added activities, you can streamline the process and make it more efficient. This means less wasted time during changeovers and more time spent on actual production.
-
Reduced Costs: Set-up time often results in wasted resources such as labor, energy, and materials. By reducing this time, you can minimize these costs and improve overall profitability.
-
Increased Flexibility: With shorter setup times, you can quickly switch between different products or variations without sacrificing quality or efficiency. This allows you to respond faster to customer demands and market changes.
-
Enhanced Quality Control: During longer setup times, errors or defects may go unnoticed until production starts again. By minimizing this transition period, you can identify any issues sooner and ensure better quality control throughout the entire production process.
By incorporating SMED techniques into your lean manufacturing strategy, you can optimize your set-up processes and reap the benefits of reduced downtime, improved efficiency, cost savings, increased flexibility, and enhanced quality control.
Measuring and Monitoring Key Performance Indicators
Measuring and monitoring key performance indicators allows you to track progress and make data-driven decisions for continuous improvement in your organization. By implementing lean manufacturing principles, you can identify the most important metrics that align with your business goals. These key performance indicators (KPIs) provide valuable insights into the efficiency and effectiveness of your processes, helping you identify areas for improvement. Some common KPIs in lean manufacturing include cycle time, defect rate, and overall equipment effectiveness (OEE). Tracking these metrics enables you to measure your current performance against desired targets and benchmarks, allowing you to take proactive steps towards achieving operational excellence. Regularly monitoring these KPIs also helps create a culture of accountability within your organization, as everyone becomes aware of their impact on overall performance.
Frequently Asked Questions
How can lean manufacturing principles be applied to service-based industries?
To apply lean manufacturing principles to service-based industries, you can focus on eliminating waste, improving processes, and enhancing customer value. This will help streamline operations and increase efficiency in delivering services to customers.
What are some common challenges companies face when implementing lean manufacturing practices?
Implementing lean manufacturing practices can be challenging for companies. In fact, a study found that 60% of organizations face resistance from employees during the implementation process, hindering their progress and success.
How can lean manufacturing contribute to environmental sustainability?
Lean manufacturing practices can contribute to environmental sustainability by reducing waste, energy consumption, and carbon emissions. By implementing efficient processes and promoting recycling, companies can minimize their environmental impact and create a more sustainable future.
Are there any specific industries or sectors where lean manufacturing is not suitable?
There are certain industries or sectors where lean manufacturing may not be suitable. Factors such as complex production processes, high customization requirements, or low volume production can make it difficult to implement lean principles effectively.
What are some potential risks or drawbacks of implementing lean manufacturing in an organization?
Implementing lean manufacturing in an organization can have potential risks and drawbacks. These may include resistance from employees, disruption to current processes, increased pressure on resources, and the need for significant cultural change.
Disclaimer: Some information is provided through AI. Users should always conduct their own research and consult with qualified professionals before making any decisions.Related Posts

Try Now
ServiceFolder's field service scheduling software free plan is perfect for small businesses with up to three people or less. It includes time tracking, scheduling, and mobile app features that make it one of the best mobile field service management software solutions for small businesses available. It is perfect for any small business company within the field service industry that wants to use technology to increase performance and productivity.