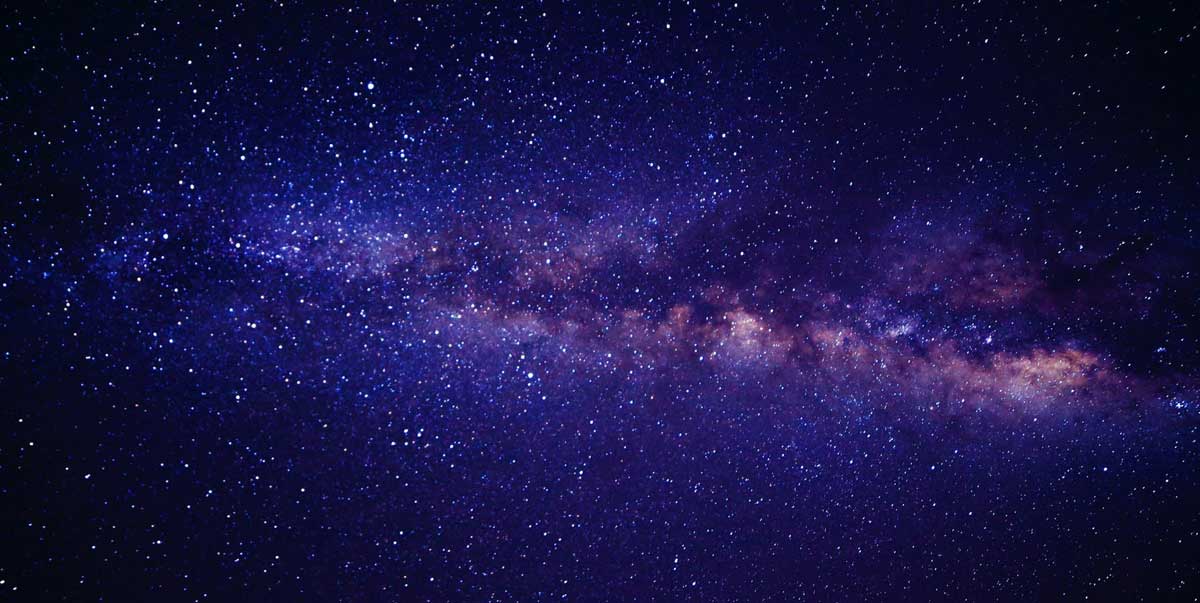
Forklift Pm
Are you looking to maximize the lifespan and efficiency of your forklifts? If so, then implementing a comprehensive forklift preventive maintenance (PM) program is essential. Forklift PM involves regular inspections, servicing, and repairs to ensure that your forklifts are in top-notch condition and operating at their best. By following a proactive approach to maintenance, you can avoid costly breakdowns, minimize downtime, and enhance safety in your workplace.
In this article, we will delve into the world of forklift PM and provide you with valuable insights on creating a maintenance plan tailored to your specific needs. We will walk you through the process of conducting stationary and mobile checklists, highlighting the critical areas that need attention during each inspection. Moreover, we will discuss how preventive maintenance can increase the lifespan of your forklifts and save you money in the long run. So buckle up and get ready to learn everything you need to know about forklift PM!
ServiceFolder's Field Service Management Software provides complete software solutions for back office and field service technicians for the Equipment Maintenance Businesses.
Forklift Preventive Maintenance Overview
Forklift PM is crucial for ensuring the smooth operation and longevity of your equipment, as the saying goes, “An ounce of prevention is worth a pound of cure.”Regular maintenance and inspections are essential to keep your forklift in optimal condition. By implementing a preventive maintenance program, you can identify any potential issues before they become major problems. This includes checking fluid levels, inspecting tires, brakes, and forks for any signs of wear or damage. It is also important to train operators on proper forklift handling techniques to prevent accidents and promote safety. A well-executed forklift preventive maintenance program not only extends the lifespan of your equipment but also enhances operational efficiency while prioritizing safety measures.
Creating a Maintenance Plan
Make sure you’re creating a maintenance plan that outlines regular check-ups and repairs for your forklift PM. Preventive maintenance is crucial in ensuring the longevity and optimal performance of your forklift. When creating a maintenance plan, it’s important to consider all the components of the forklift that require routine inspections and servicing. This includes checking the engine, hydraulic systems, brakes, tires, and other vital parts. A well-structured maintenance schedule should be established to ensure timely inspections and necessary repairs are carried out. By adhering to a proper maintenance plan, you can identify potential issues before they become major problems, minimizing downtime and improving overall safety in the workplace.
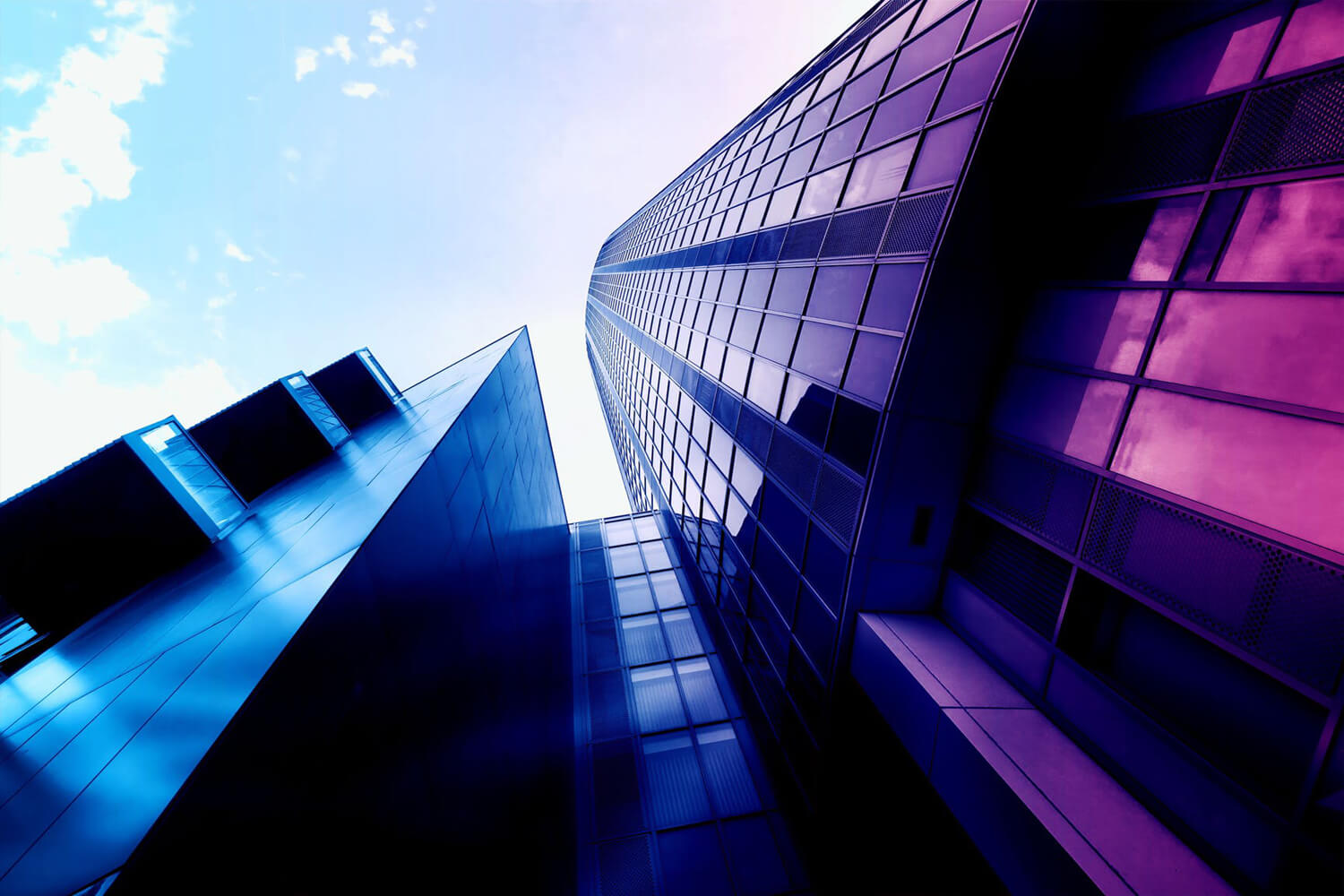
Discover more ServiceFolder Features for your
Equipment Maintenance Businesses
Contact Us
Free - 1 User
Stationary Checklist
Before you begin your work, it’s crucial to ensure that all the necessary items on the stationary checklist have been completed. This checklist is an essential part of your forklift PM and maintenance plan, as it helps you keep track of important tasks and ensure that your equipment is in optimal condition. Here are four key items that should be included on this checklist:
- Inspect the forklift body for any signs of damage or wear. This includes checking the forks, mast, tires, and other components to ensure they are in good working order.
- Check all fluid levels, including oil, coolant, hydraulic fluid, and brake fluid. It’s important to maintain proper levels to prevent any potential issues or breakdowns during operation.
- Test all safety features such as lights, horn, seatbelt, and backup alarms. These features are critical for maintaining a safe working environment and preventing accidents.
- Verify that all scheduled maintenance tasks have been completed according to the manufacturer’s recommendations. This may include replacing filters or belts, lubricating moving parts, or inspecting electrical connections.
By completing these tasks on your stationary checklist before starting your work, you can help prevent unexpected breakdowns and ensure that your fleet operates smoothly. Remember that regular planned maintenance is key to prolonging the lifespan of your equipment and minimizing downtime. If you notice any issues during your inspection or if a task has not been completed properly, be sure to notify a qualified technician who can address them promptly.
Mobile Checklist
Once you’re ready to hit the floor, don’t forget to grab your mobile checklist to ensure that all necessary tasks are completed for a smooth and efficient operation. The mobile checklist is an essential tool for performing preventive maintenance (PM) on your forklift. It allows you to keep track of important tasks such as checking the battery condition, inspecting the tires and brakes, and identifying any fluid requirements. By following this checklist, you can ensure that your powered lift is in optimal working condition, reducing the risk of breakdowns and maximizing productivity. So before you start operating your forklift, make sure to go through the mobile checklist and address any issues that may arise.
Get started with ServiceFolder
- Manage Jobs & Staff
- On Site Quote and Invoice
- On Site Notes and Photos
- Sync with Quickbooks Online
- Print Designer for all Documents
- Equipment/Asset Management
- Customer Management
- Leads Management
- Inventory Management
- Customer Notifications
- Customer Fields
- PriceBooks
Increasing Forklift Lifespan
To maximize the lifespan of your forklift, it’s crucial to prioritize regular maintenance and address any potential issues promptly. By following a proactive approach to forklift PM (preventative maintenance), you can ensure that your equipment remains in optimal condition for years to come. Here are some key steps you can take to increase the lifespan of your forklift:
- Regularly check and maintain the battery condition, as a well-maintained battery not only prolongs the overall lifespan but also enhances the performance of your forklift.
- Perform proper repairs whenever necessary, addressing any minor issues before they escalate into major problems. This will not only prevent costly breakdowns but also save on operating costs in the long run.
- Implement a comprehensive preventative maintenance program that includes routine inspections, lubrication, and cleaning. This will help identify potential issues early on and prevent them from becoming more severe over time.
- Train your operators on proper forklift operation techniques, including how to handle loads safely and avoid unnecessary wear and tear on the equipment. By educating your team on best practices, you can minimize damage caused by operator error and extend the overall lifespan of your forklift.
PM Frequency
Regularly maintaining your forklift is like giving it a check-up, ensuring that it remains in top shape and performs at its best. One crucial aspect of forklift maintenance is determining the frequency of preventive maintenance (PM) tasks. PM frequency refers to how often you should carry out maintenance activities on your forklift to prevent breakdowns and ensure it operates properly. The ideal PM frequency depends on various factors such as the type of forklift, its usage intensity, and the manufacturer’s recommendations. Generally, it is recommended to conduct routine PM checks on a monthly basis or after every 200 hours of operation. However, keep in mind that more frequent inspections may be necessary if your forklift operates in harsh or demanding conditions. By adhering to a regular PM schedule, you can significantly increase the lifespan of your forklift and ensure that it continues to function effectively and safely over time.
Try all in one Equipment Maintenance Businesses Software - Free - 1 UserPM Duration
Maintaining your forklift at its best means considering the duration of preventive maintenance (PM) tasks, ensuring optimal performance and longevity. When it comes to PM duration, it is important to have a well-planned schedule that takes into account the specific needs of your forklift and the demands of your facility. Here are some key points to keep in mind:
-
Regular Inspection: Conducting regular inspections helps identify any potential issues before they become major problems. This can include checking fluid levels, inspecting tires for wear and tear, and examining crucial components like brakes and hydraulics.
-
Lubrication: Proper lubrication is essential for smooth operation and preventing premature wear on moving parts. Be sure to follow the manufacturer’s recommendations regarding the frequency and type of lubricant to use.
-
Component Replacement: Certain components, such as filters or belts, may need to be replaced at specific intervals. Keeping track of these replacement schedules ensures that your forklift continues to function efficiently.
By adhering to a well-planned PM schedule that addresses these key areas, you can maximize the lifespan of your forklift while minimizing costly breakdowns and downtime. Remember that each forklift may have unique maintenance requirements based on factors such as usage intensity or operating conditions.
Preventive Maintenance Schedule
Make sure you have a well-organized maintenance plan in place to keep your lift truck in top shape and avoid any unnecessary disruptions. Forklift preventive maintenance schedule is crucial for the smooth operation of your powered lift truck. Regular inspections and servicing will help identify any issues before they turn into major problems. It is important to check the battery condition, tire pressure, brake functionality, and fluid levels regularly. This should be done as part of an operating daily routine to ensure optimal performance and safety. Additionally, make sure to follow the manufacturer’s guidelines for maintenance intervals and procedures specific to your forklift model. By sticking to a preventive maintenance schedule, you can extend the lifespan of your forklift and minimize costly repairs or downtime due to unexpected breakdowns or malfunctions.
Benefits of Preventive Maintenance
One of the key advantages of implementing a preventive maintenance plan is that it can significantly reduce unexpected repair costs and minimize downtime. By conducting regular maintenance on your forklifts, you can identify and address potential issues before they escalate into major problems. This proactive approach helps to prevent breakdowns and costly repairs, keeping your forklifts operating at their optimal level. Additionally, preventive maintenance improves the overall lifespan of your forklifts, ensuring they have a longer service life and reducing the need for frequent replacements. To give you an idea of the benefits of preventive maintenance, here is a table showcasing some specific advantages:
Benefits | Description |
---|---|
Cost Savings | Regular maintenance helps prevent expensive repairs and extends the lifespan of your forklifts. |
Increased Efficiency | Well-maintained forklifts operate more efficiently, resulting in improved productivity and reduced costs. |
Safety Improvements | Preventive maintenance ensures that all safety features are functioning correctly, minimizing accidents. |
Compliance with Laws | Regular inspections and maintenance help you meet regulatory requirements and avoid penalties or fines. |
By incorporating preventative maintenance into your forklift PM schedule, you can enjoy these benefits while also ensuring smooth operations and reducing any unforeseen disruptions or expenses related to equipment failure.
Areas Checked During Maintenance
To ensure smooth operations and minimize any unexpected disruptions, you’ll be thrilled to know that our maintenance experts thoroughly inspect various critical areas during routine check-ups. Here are the four areas that they pay close attention to:
- Battery condition: Our experts check the battery to ensure it is in good working order and has enough power to operate the forklift efficiently.
- Fluid levels: They make sure that all necessary fluids, such as hydraulic fluid and coolant, are at the correct levels for optimal performance.
- Hose inspection: Our team carefully inspects all hoses for any signs of leaks or damage, as these can lead to potential breakdowns or safety hazards.
- Tire and brake examination: They assess the tire tread depth and overall condition to ensure proper traction and stability, while also inspecting the brakes for any signs of wear or malfunction.
By meticulously examining these crucial components - battery, fluid levels, hoses, tires, and brakes - our maintenance experts can identify any potential issues early on and address them promptly. This proactive approach helps to prevent costly repairs or unexpected downtime in your operations.
Disclaimer: Some information is provided through AI. Users should always conduct their own research and consult with qualified professionals before making any decisions.Related Posts

Try Now
ServiceFolder's field service scheduling software free plan is perfect for small businesses with up to three people or less. It includes time tracking, scheduling, and mobile app features that make it one of the best mobile field service management software solutions for small businesses available. It is perfect for any small business company within the field service industry that wants to use technology to increase performance and productivity.