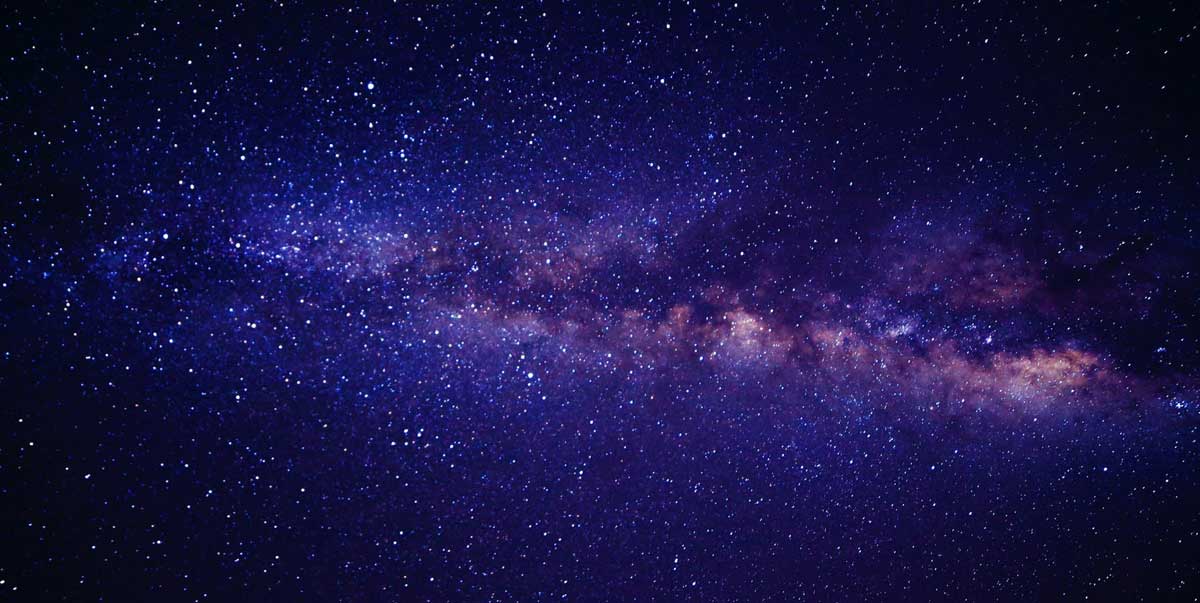
Equipment Maintenance Management Software
Are you tired of the endless cycle of equipment breakdowns and repairs? Are you struggling to keep track of maintenance schedules and histories? It’s time to consider investing in equipment maintenance management software.
With this software, you can streamline your entire maintenance process, from tracking maintenance history to scheduling preventative tasks. You’ll receive alerts for upcoming maintenance and be able to identify equipment in need of repair or replacement. Not only will this improve overall equipment performance, but it will also enhance safety and compliance measures. Plus, automation saves both time and money in the long run. So let’s dive into why choosing the right equipment maintenance management software is crucial for any business that relies on machinery and assets.
ServiceFolder's Field Service Management Software provides complete software solutions for back office and field service technicians for the Equipment Maintenance Businesses.
Streamlining Your Equipment Maintenance Process
By streamlining your equipment maintenance process, you’ll feel like you have an army of robots working tirelessly to keep everything running smoothly. Benefits of automation are numerous, including reduced downtime and improved productivity. With equipment maintenance management software, you can automate tasks such as scheduling maintenance checks and generating work orders. This not only saves time but also reduces the risk of human error. Efficiency improvement techniques such as predictive maintenance can also be implemented with the help of this software. By analyzing data from your equipment, it can predict when a part is likely to fail and schedule maintenance before it becomes a problem. Overall, implementing an equipment maintenance management software can greatly improve your efficiency and save you both time and money in the long run.
Tracking Maintenance History with Ease
Keeping track of the past repairs and check-ups is a breeze with this tool. The equipment maintenance management software allows you to easily view the maintenance history of each piece of equipment in your inventory. With customizable reports at your fingertips, you can quickly gather data on how often specific machines require maintenance or repairs. The user-friendly interface makes it easy for even non-technical users to access and interpret the information, giving you valuable insights into your equipment’s performance. Plus, with all this information in one place, you can make informed decisions about when to schedule preventative maintenance or replace aging equipment.
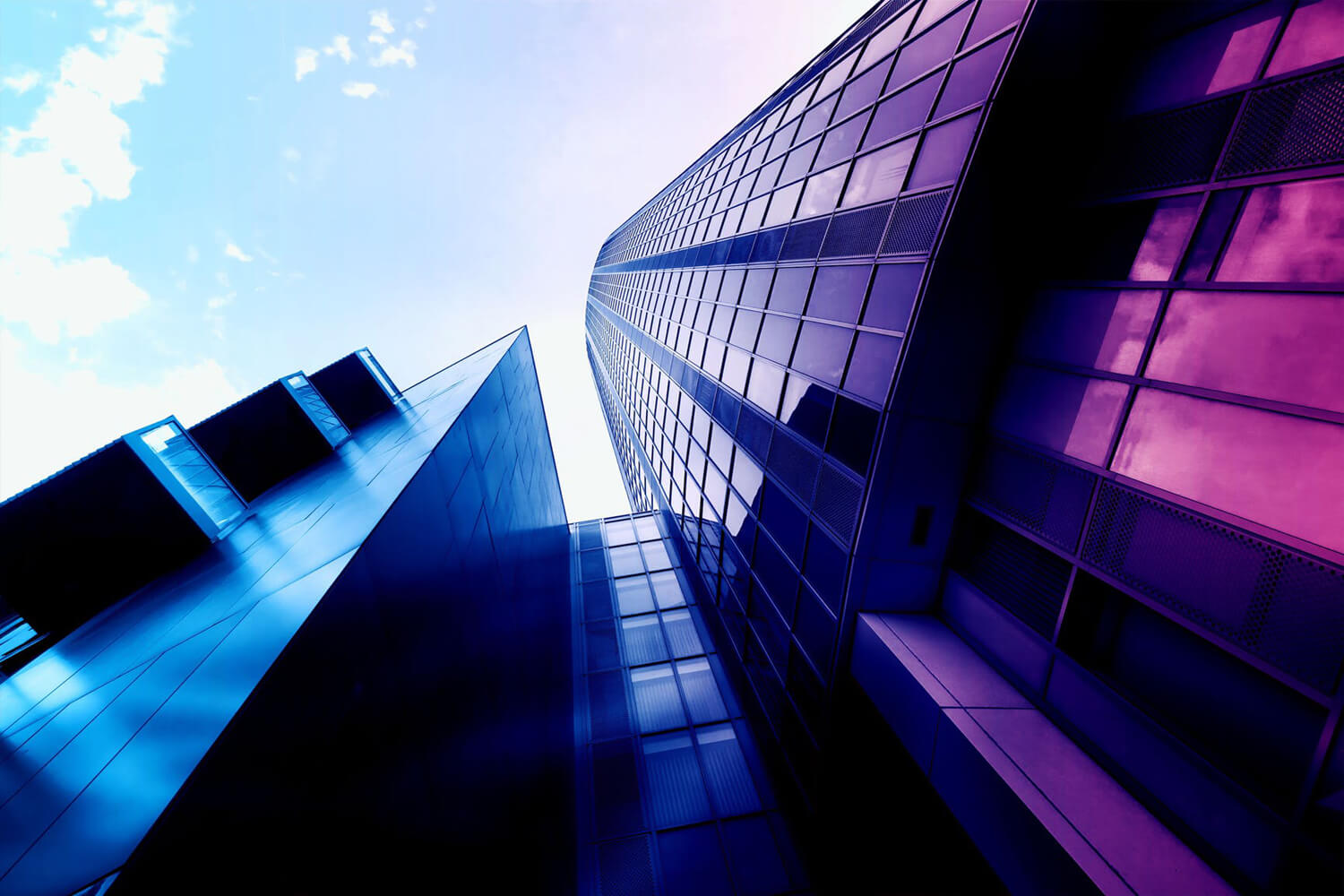
Discover more ServiceFolder Features for your
Equipment Maintenance Businesses
Contact Us
Free - 1 User
Scheduling Preventative Maintenance Tasks
Scheduling preventative maintenance tasks is made effortless with the intuitive interface of this tool. By using preventative maintenance, you are able to prolong equipment life and reduce unexpected downtime. With the software’s scheduling best practices, you can create a plan that works for your business needs and automatically generate work orders based on time or usage. This not only saves time but ensures that all necessary tasks are completed on schedule. The benefits of preventative maintenance are numerous: it reduces costly repairs, improves safety, and increases productivity by ensuring that your equipment is functioning optimally at all times. To emphasize this point further, take a look at the table below:
Benefit | Explanation |
---|---|
Reduced repairs | Preventative maintenance catches issues before they become major problems, reducing repair costs |
Improved safety | Regularly maintaining equipment increases safety by identifying potential hazards before they occur |
Increased productivity | Consistent upkeep ensures optimal efficiency and productivity from equipment |
By following these best practices and utilizing the software’s scheduling capabilities, you can ensure that your equipment stays in top shape while minimizing unexpected downtime and maximizing ROI.
Receiving Alerts for Upcoming Maintenance
Get notified of upcoming maintenance with easy-to-set alerts, ensuring that you never miss a scheduled check-up or inspection. With customizable notifications, you can set alerts for specific equipment, parts, or tasks, giving you the flexibility to manage your maintenance schedule efficiently. Maintenance scheduling optimization is made possible by receiving alerts for upcoming maintenance; this feature allows you to plan ahead and avoid downtime caused by unexpected equipment failures. Moreover, setting reminders can help improve safety compliance and reduce liability risks associated with missed inspections or repairs. Lastly, automated alerts save time and increase productivity by eliminating the need for manual monitoring of schedules and deadlines.
Get started with ServiceFolder
- Manage Jobs & Staff
- On Site Quote and Invoice
- On Site Notes and Photos
- Sync with Quickbooks Online
- Print Designer for all Documents
- Equipment/Asset Management
- Customer Management
- Leads Management
- Inventory Management
- Customer Notifications
- Customer Fields
- PriceBooks
Identifying Equipment in Need of Repair or Replacement
Sometimes, when the wheels on a car start to squeak and wobble, it’s a sign that they may need to be repaired or replaced. Similarly, equipment inspection is crucial in identifying machinery that needs repair or replacement. Maintenance assessment helps to determine whether equipment is still functioning optimally or if it needs attention. With an equipment maintenance management software, you can track all your equipment and receive alerts for upcoming maintenance tasks. Using a table like the one below can help you quickly identify which equipment needs attention so you can take action before it causes any downtime.
Equipment Name | Last Inspection | Next Maintenance |
---|---|---|
Conveyor Belt #1 | 01/01/2021 | 07/01/2021 |
Forklift #2 | 02/15/2021 | 08/15/2021 |
Packaging Machine #3 | 03/20/2021 | 09/20/2021 |
By keeping track of your equipment with an EMMS, you ensure that all your machinery runs smoothly and efficiently without unexpected breakdowns or repairs.
Reducing Downtime and Associated Costs
Minimizing downtime and associated costs is key to keeping your operations running smoothly and maximizing profits. To achieve this, here are four tips for reducing downtime and associated costs with equipment maintenance management software: 1) Implement root cause analysis to identify the underlying issues causing downtime and address them proactively. 2) Use predictive maintenance techniques to anticipate potential problems before they occur, avoiding unexpected downtime. 3) Make sure your employees are trained on how to properly operate and maintain equipment to prevent breakdowns caused by user error. 4) Keep detailed records of all repairs, inspections, and maintenance activities to help you track patterns of equipment failure and make data-driven decisions about when it’s time for repair or replacement. By following these guidelines, you can reduce downtime, increase productivity, and ultimately save money in the long run.
Try all in one Equipment Maintenance Businesses Software - Free - 1 UserImproving Overall Equipment Performance
To boost your overall equipment performance, you’ll need to take a proactive approach and keep an eye on potential issues before they cause problems. Maximizing uptime is crucial for any business, and one way to achieve this is by optimizing maintenance strategies. Using tools like predictive maintenance or condition monitoring can help you stay ahead of the curve and avoid unexpected downtime. By regularly analyzing data and identifying trends, you can make informed decisions about when to perform maintenance tasks and avoid costly repairs in the future. Investing in equipment maintenance management software can also streamline your processes and ensure that all necessary tasks are completed on time. With a focus on improving overall equipment performance, you can increase productivity, reduce costs, and ultimately achieve greater success for your business.
Enhancing Safety and Compliance Measures
You can prioritize the safety of your workers and ensure compliance with regulations by implementing effective training programs and regularly reviewing and updating your procedures. To enhance safety measures, consider the following:
- Importance of Employee Training:
- Train employees on proper equipment use and maintenance to prevent accidents.
- Provide regular safety training to ensure that employees are always aware of potential hazards.
- Implementing Safety Protocols:
- Review your current safety protocols to identify areas for improvement.
- Update your procedures regularly to reflect changes in regulations and industry standards. By focusing on employee training and implementing effective safety protocols, you can reduce the risk of accidents, protect your workforce, and stay compliant with regulations.
Saving Time and Money with Automation
Now that you understand the importance of enhancing safety and compliance measures, it’s time to talk about how automation can save you both time and money. With automated maintenance tracking through equipment maintenance management software, you can easily keep track of all your maintenance needs without having to manually input data. This means fewer errors and less time spent on paperwork. In addition, many software solutions offer cost-effective maintenance solutions by helping you identify potential issues before they become major problems, allowing for timely repairs and replacements that prevent downtime and costly repairs. Take a look at the table below to see some examples of how automated maintenance tracking can benefit your business.
Benefit | Explanation | Example |
---|---|---|
Time Savings | Automated tracking eliminates manual data entry, saving time spent on paperwork. | A company with 50 pieces of equipment could save up to 30 hours per week by automating their maintenance tracking system. |
Cost Savings | Early identification of potential issues allows for timely repairs or replacements that prevent downtime and costly repairs. | A manufacturing plant was able to reduce their repair costs by 20% in one year after implementing an automated maintenance tracking system. |
Improved Efficiency | Automated systems allow for easy scheduling of routine maintenance tasks, improving overall efficiency. | An aviation company was able to increase their productivity by 15% after implementing an automated system for tracking aircraft maintenance schedules. |
By utilizing equipment maintenance management software with automated tracking features, businesses can save both time and money while improving overall efficiency. Don’t let manual data entry hold you back - make the switch today!
Choosing the Right Equipment Maintenance Management Software
Take a moment to consider the perfect solution for streamlining your equipment upkeep and ensuring smooth operations. When choosing the right equipment maintenance management software, it’s important to look for customization options that fit your specific needs. You want a platform that can adapt to your unique requirements and processes, rather than having to conform to a one-size-fits-all solution. Additionally, integration capabilities are key in making sure all aspects of your maintenance program are seamlessly integrated into one system. This allows you to have full visibility and control over every aspect of your equipment maintenance, from work order creation to inventory tracking and beyond. By choosing the right software with these features, you can significantly improve efficiency, reduce downtime and ultimately save time and money in the long run.
Frequently Asked Questions
Can the software be integrated with other business management systems?
Yes, the software has integration capabilities and can be easily integrated with other business management systems. Compatibility concerns are minimal as it supports various platforms and APIs.
What types of equipment can be managed with the software?
You can manage industrial equipment and fleet vehicles with our software. It simplifies the maintenance process, tracks usage and repairs, and ensures compliance with safety regulations.
Is there a mobile app available for technicians to access the software on-the-go?
You’ll be pleased to know that technician accessibility is a top priority for us. With our mobile functionality, technicians can access everything they need on-the-go. No more being tethered to a desk!
Can the software generate reports and analytics on equipment maintenance performance?
You can easily access reports and analytics on equipment maintenance performance with data visualization. Additionally, using predictive maintenance will allow you to anticipate issues and resolve them before they become larger problems.
Is there training and support available for implementing and using the software?
Imagine embarking on a journey without a map or guide. Training effectiveness and user adoption rate are crucial to successful implementation of any software. Our support team is here to ensure your success.
Conclusion
Congratulations! You now know the benefits of using equipment maintenance management software. By streamlining your maintenance process, tracking history, scheduling preventative tasks, and receiving alerts for upcoming maintenance, you can improve overall equipment performance while enhancing safety and compliance measures.
But why stop there? Imagine being able to identify equipment in need of repair or replacement before it causes a major breakdown. Picture saving time and money by automating tedious tasks and having a system that does the work for you. All this is possible with the right maintenance management software.
So ask yourself: do you want to continue struggling with manual processes and risking costly downtime? Or do you want to take control of your equipment maintenance with an efficient and reliable solution? The choice is yours.
Disclaimer: Some information is provided through AI. Users should always conduct their own research and consult with qualified professionals before making any decisions.Related Posts

Try Now
ServiceFolder's field service scheduling software free plan is perfect for small businesses with up to three people or less. It includes time tracking, scheduling, and mobile app features that make it one of the best mobile field service management software solutions for small businesses available. It is perfect for any small business company within the field service industry that wants to use technology to increase performance and productivity.