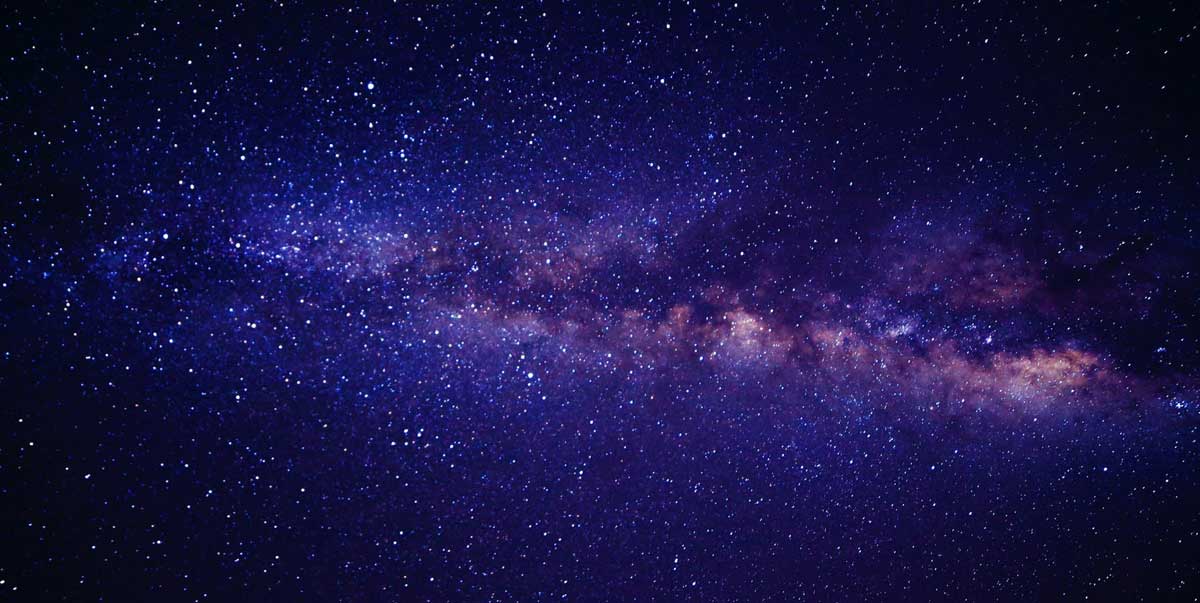
Commercial Equipment Service Software
Are you tired of dealing with the headaches that come with equipment maintenance? Keeping track of routine tasks, monitoring performance, and ordering replacement parts can be a daunting task for any business owner. But fear not, commercial equipment service software is here to help streamline your management processes and keep your equipment running smoothly.
With the right service software, you can easily schedule and track routine maintenance tasks, monitor equipment performance and repair history, manage inventory and order replacement parts - all in one place. This not only maximizes efficiency but also minimizes downtime for your business. Read on to learn more about the importance of proper equipment maintenance, common challenges in equipment management, and key features to look for when choosing the right service software for your business.
ServiceFolder's Field Service Management Software provides complete software solutions for back office and field service technicians for the Equipment Maintenance Businesses.
The Importance of Proper Equipment Maintenance
Proper equipment maintenance is crucial for keeping your machines running smoothly and avoiding costly repairs down the line. By implementing regular preventive maintenance, you can catch small issues before they become bigger problems that require expensive repairs or even replacement of the equipment. This not only saves you money in the long run but also extends the lifespan of your equipment, allowing you to get more use out of it and maximize your investment. Neglecting proper maintenance can lead to breakdowns, disrupted operations, and increased downtime which can negatively impact your business’s productivity and profitability. Therefore, investing in a commercial equipment service software to help manage and schedule maintenance tasks can be a wise decision for any business owner who wants to ensure their machinery remains in optimal condition.
Common Challenges in Equipment Management
Managing machines can be a tricky business, especially when you’re dealing with unexpected breakdowns and maintenance issues. Here are three common challenges in equipment management that you may face: 1) Equipment tracking - it can be overwhelming to keep track of all the machines and their locations within your facility. This is where commercial equipment service software can come in handy by providing real-time updates on equipment whereabouts. 2) Maintenance scheduling - scheduling regular maintenance for each machine can be time-consuming and difficult to coordinate. With the help of software, you can easily schedule maintenance tasks based on usage data and avoid breakdowns caused by neglecting routine upkeep. 3) Predictive maintenance - predicting when a machine will fail before it actually does is challenging but critical for preventing costly downtime. Commercial equipment service software uses advanced analytics to detect patterns in machine performance, allowing you to predict failures and take proactive measures before they occur.
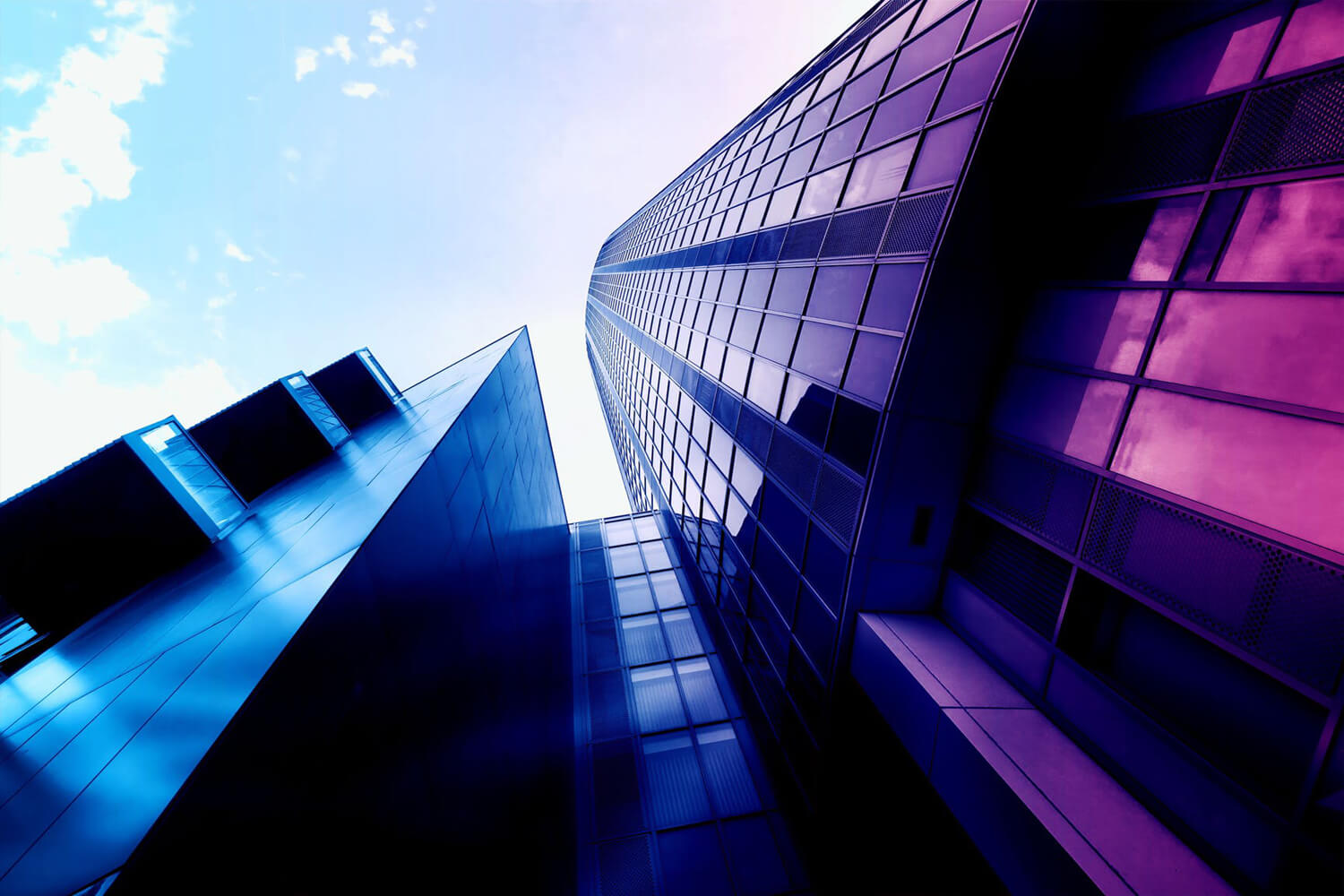
Discover more ServiceFolder Features for your
Equipment Maintenance Businesses
Contact Us
Free - 1 User
Understanding Commercial Equipment Service Software
Get ready to streamline your equipment maintenance process with the help of user-friendly commercial equipment service software that offers a range of benefits. With this software, you can easily schedule preventative maintenance tasks and track repair history, reducing the risk of unexpected breakdowns and costly downtime. Additionally, the software provides real-time updates on equipment performance metrics, enabling you to optimize productivity and identify areas for improvement. While implementing this software may present some challenges, such as integrating it with existing systems or training staff on its use, these hurdles can be overcome with proper planning and support from your vendor. Overall, investing in commercial equipment service software is a smart choice for any business looking to increase efficiency and reduce costs in their equipment management processes.
Key Features of Effective Service Software
You’ll be pleased to know that effective service software includes several key features that can help you streamline your maintenance processes and improve equipment performance. Did you know that according to recent studies, companies using service software experience an average of 28% reduction in unplanned downtime? To achieve these benefits, look for software with integration capabilities that allow it to connect with other systems and devices, such as sensors or IoT platforms. A user interface design that’s intuitive and easy-to-use is also essential for quick adoption by your team members. Other important features include real-time monitoring and reporting, mobile accessibility for on-the-go updates, and customizable workflows tailored to your specific needs. By choosing a service software solution with these key features, you can significantly enhance the efficiency of your maintenance operations while reducing costly downtime and maximizing equipment performance.
Get started with ServiceFolder
- Manage Jobs & Staff
- On Site Quote and Invoice
- On Site Notes and Photos
- Sync with Quickbooks Online
- Print Designer for all Documents
- Equipment/Asset Management
- Customer Management
- Leads Management
- Inventory Management
- Customer Notifications
- Customer Fields
- PriceBooks
Choosing the Right Service Software for Your Business
Finding the perfect solution for your business can be a challenge, but when it comes to selecting service software, there are key factors to consider. Two of the most important things you should think about are customization options and cost benefit analysis. You want a software that can be tailored to fit your specific needs and preferences, without having to pay for features you don’t need. A good way to evaluate this is by doing a cost benefit analysis, which involves comparing the costs of potential solutions against their expected benefits in order to determine which one offers the best value for your business. To help you make an informed decision, check out the table below that highlights some of the key differences between customizable and non-customizable service software options.
Setting Up Your Service Software System
Once you’ve decided on the best service software solution for your business, it’s important to set it up properly to ensure optimal functionality and efficiency. To do this, start by setting up service contracts within the system. This will allow you to easily track and manage all of your clients’ needs and ensure that they are receiving the appropriate level of service. Next, optimize your workflow by customizing the software to fit your specific business needs. This may include creating automated processes for tasks such as scheduling appointments or generating invoices. Finally, make sure that all employees are trained on how to use the software effectively so that everyone is on the same page and can work together seamlessly. By taking these steps, you can maximize the benefits of your commercial equipment service software and streamline your operations for greater success.
Try all in one Equipment Maintenance Businesses Software - Free - 1 UserScheduling and Tracking Routine Maintenance Tasks
Efficiently scheduling and tracking routine maintenance tasks is crucial for keeping your equipment running smoothly and avoiding costly breakdowns. Preventive maintenance is the key to ensuring that your commercial equipment operates at peak performance levels. This involves setting up a maintenance schedule, which should be optimized based on factors such as equipment usage, manufacturer recommendations, and historical data. With the right service software system in place, you can easily track when each piece of equipment is due for maintenance, assign technicians to perform the work, and ensure that all tasks are completed on time. By staying on top of routine maintenance tasks, you can minimize downtime and extend the lifespan of your valuable assets.
Monitoring Equipment Performance and Repair History
To really understand how your assets are performing and to anticipate future problems, you’ll need to be able to monitor their performance and repair history closely. By tracking efficiency metrics such as uptime, energy consumption, and maintenance costs over time, you can identify trends that signal potential issues before they become critical. Additionally, keeping detailed records of past repairs allows you to quickly diagnose recurring problems and plan for preventative maintenance accordingly. With this information at your fingertips, you can take proactive steps towards predicting failures and minimizing downtime for your commercial equipment.
Managing Inventory and Ordering Replacement Parts
As you manage your inventory and order replacement parts, it’s like playing a game of chess - anticipating potential moves and making strategic decisions to keep your assets running smoothly. With the help of commercial equipment service software, inventory tracking becomes a breeze. You can easily monitor stock levels and set reorder points to ensure you never run out of critical items. Additionally, supplier management is streamlined with the ability to track vendor information, pricing, and lead times all in one place. This allows you to make informed purchasing decisions and negotiate better deals with suppliers. The following table shows how easy it is to manage inventory using commercial equipment service software:
Feature | Description |
---|---|
Inventory Tracking | Keep track of stock levels for all parts and supplies |
Reorder Points | Set minimum stock levels for automatic reordering |
Vendor Management | Store vendor contact information, pricing, and lead times |
Purchase Orders | Create purchase orders directly from inventory tracking system |
With these capabilities at your fingertips, managing inventory and ordering replacement parts has never been easier or more efficient than with commercial equipment service software.
Maximizing Efficiency and Minimizing Downtime with Service Software
By using service software, you can ensure your business runs smoothly and experiences minimal downtime. Here are three ways that utilizing this technology can increase productivity while reducing costs: 1) Service software automates many administrative tasks, such as scheduling appointments or generating work orders, freeing up time for technicians to focus on more critical issues. 2) With real-time access to customer information and equipment history, technicians can diagnose problems more efficiently and accurately, leading to faster resolution times. 3) By tracking inventory levels and usage trends, service software can help businesses optimize their stock levels and reduce waste from over-ordering or under-utilization of parts. Overall, investing in commercial equipment service software is a smart move for any business looking to streamline its operations and improve its bottom line.
Frequently Asked Questions
What are some common misconceptions about commercial equipment service software?
Hey there! One common misconception is that service software is only for large corporations. In reality, it benefits businesses of all sizes with features like streamlined scheduling and inventory tracking.
How can service software be integrated with other software systems in a business?
To integrate service software with other systems, ensure compatibility and data integration. Determine what data needs to be shared between systems and establish a protocol for transferring information seamlessly.
What are some best practices for training employees on new service software?
When training employees on new software, it’s important for trainers to understand their role in providing effective instruction. Encouraging employee feedback and engagement can also improve the learning experience and increase retention rates.
Can service software be customized to meet specific business needs?
Oh, of course not! Service software can’t possibly be customized to meet specific business needs. Why bother with the benefits of customization and meeting industry requirements when you can just use generic software?
How does service software handle emergency repairs or unplanned maintenance tasks?
When faced with emergency repairs or unplanned maintenance tasks, you need to prioritize them based on urgency. Real time communication helps to quickly dispatch the right technician, ensure timely resolution and avoid downtime.
Conclusion
Congratulations! You’ve made it to the end of this article about commercial equipment service software. You must be feeling pretty confident now that you know all about the importance of proper equipment maintenance and the common challenges in equipment management. But let me tell you, there’s nothing quite like the thrill of unexpected breakdowns and costly repairs to keep your business on its toes!
All jokes aside, investing in effective service software can truly make a difference in maximizing efficiency and minimizing downtime for your business. So don’t wait until disaster strikes to take action - choose the right service software for your needs and start scheduling routine maintenance tasks, monitoring equipment performance, managing inventory, and ordering replacement parts today! Trust us, your future self (and your wallet) will thank you.
Disclaimer: Some information is provided through AI. Users should always conduct their own research and consult with qualified professionals before making any decisions.Related Posts

Try Now
ServiceFolder's field service scheduling software free plan is perfect for small businesses with up to three people or less. It includes time tracking, scheduling, and mobile app features that make it one of the best mobile field service management software solutions for small businesses available. It is perfect for any small business company within the field service industry that wants to use technology to increase performance and productivity.