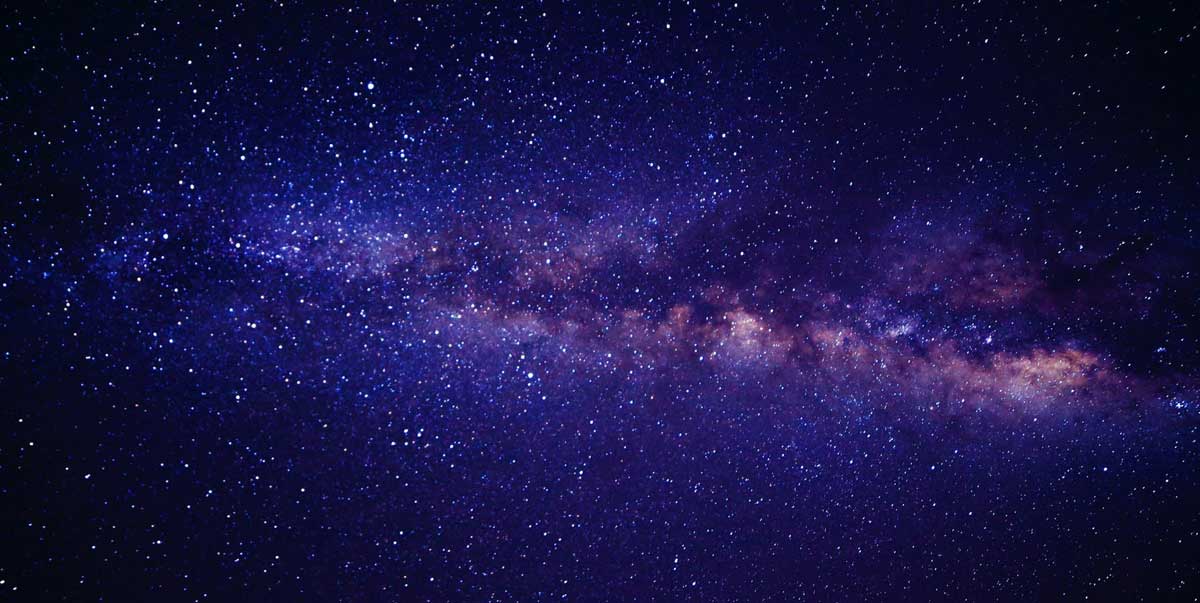
Asset Management Field Service
If you work in the field of asset management, then you understand the critical role that effective maintenance and repair services play in keeping assets functioning optimally. Asset management field service is a specialized area that requires individuals with specific skills and expertise to ensure that assets are maintained, repaired, and managed efficiently. In this article, we will explore the importance of asset management field service, essential skills for technicians working in this field, common challenges faced by professionals in this area of work, best practices for maintenance and repair of assets, leveraging technology for better asset management and future trends.
The world of asset management continues to grow as businesses invest more in their infrastructure to meet customer demands. Efficiently managing these assets can make all the difference between success or failure in meeting those demands. Asset management field service is one aspect of this process that ensures equipment runs smoothly throughout its lifespan. From routine maintenance checks to complex repairs when things go wrong - having skilled technicians who know how to manage these scenarios is crucial for any organization’s success. This article seeks to provide insights on what it takes to succeed as an asset management technician while also exploring some challenges they may face daily.
ServiceFolder's Field Service Management Software provides complete software solutions for back office and field service technicians for the Equipment Maintenance Businesses.
Understanding the Importance of Asset Management Field Service
Understanding the importance of asset management field service is key to maximizing efficiency and minimizing downtime. By implementing asset management software, you can streamline the process of tracking your assets and ensure that they are being used to their fullest potential. This not only saves time and money by reducing unnecessary repairs or replacements but also helps prevent equipment failures that could lead to costly downtime. Additionally, the benefits of asset tracking go beyond just maintenance; it can help with inventory management, improve compliance with regulations, and provide valuable data for decision-making. Overall, investing in asset management field service is a smart business move that will pay off in increased productivity and reduced costs in the long run.
Essential Skills for Asset Management Field Technicians
To excel in this role, technicians must possess a diverse skill set that enables them to tackle any challenge on the job. This includes hands-on training and customer service skills, as well as expertise in equipment troubleshooting and problem solving. In order to succeed, it is essential for asset management field technicians to be able to work independently while also collaborating effectively with team members and clients. To help cultivate these skills, many companies offer ongoing training opportunities that focus on both technical knowledge and communication strategies. By continually honing their abilities in these key areas, field technicians can provide top-notch service while also building strong relationships with customers and colleagues alike.
Skill | Importance | Emotion |
---|---|---|
Hands-on training | Critical | Confident |
Customer service skills | Essential | Empathy |
Equipment troubleshooting | Necessary | Determined |
Problem solving | Indispensable | Resourceful |
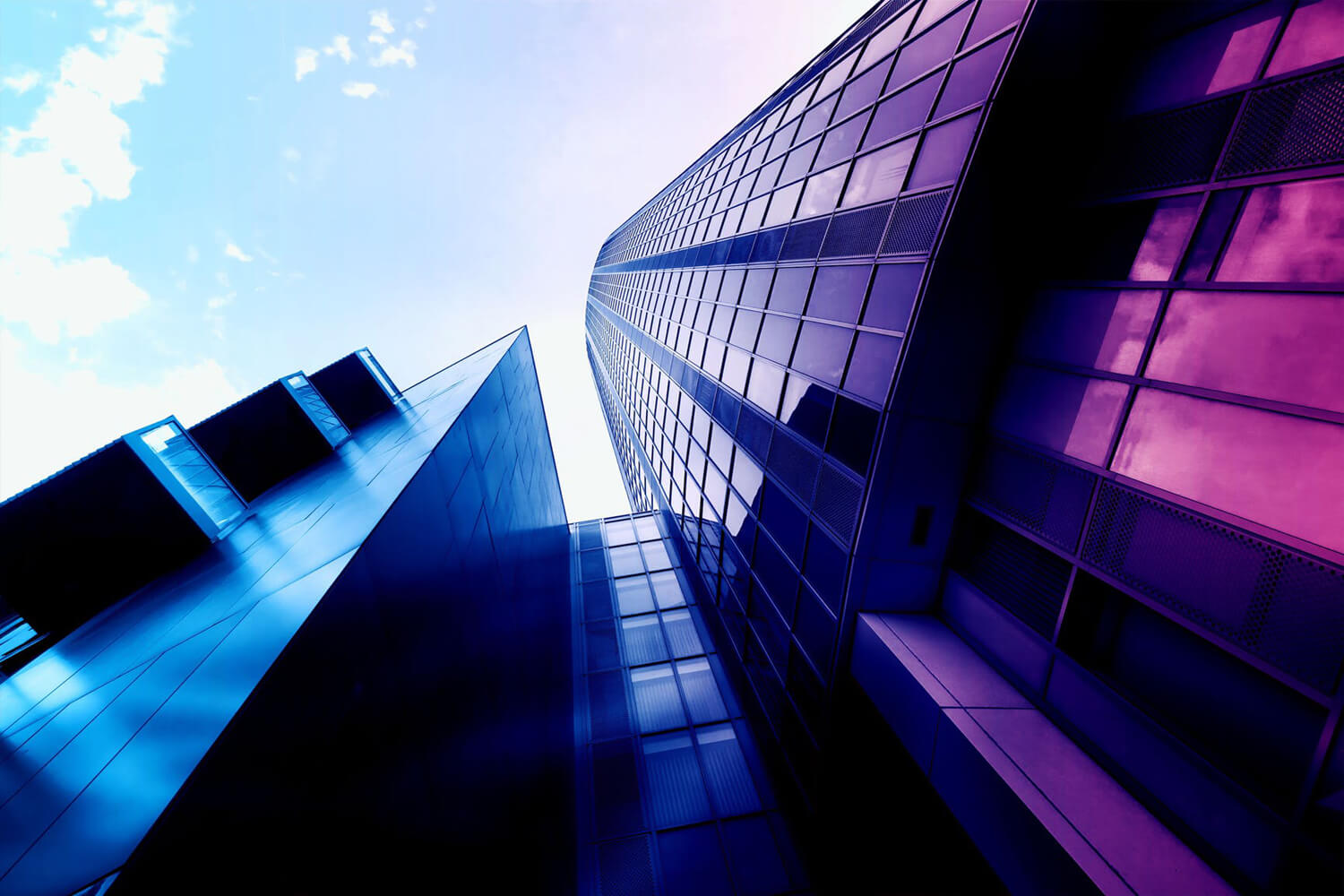
Discover more ServiceFolder Features for your
Equipment Maintenance Businesses
Contact Us
Free - 1 User
Maximizing Productivity through Effective Asset Management
By utilizing efficient practices and streamlined workflows, you can boost productivity and maximize the value of your assets. One way to do this is through data analysis. By collecting and analyzing data on asset performance, you can identify areas for improvement and implement changes to optimize processes. Another way to improve productivity is by optimizing processes themselves. This involves identifying bottlenecks in workflows and making adjustments to eliminate inefficiencies. With these strategies in place, companies can increase their bottom line while ensuring that their assets are being used to their full potential.
The Role of Organizational Skills in Asset Management Field Service
You’re missing out on major opportunities for success in asset maintenance if you don’t have your organizational skills down pat. Time management and communication skills are crucial when it comes to ensuring that all assets are properly maintained and serviced. Without these skills, it can be easy to fall behind on tasks or miss important deadlines, leading to decreased productivity and potential equipment failures. Additionally, effective problem solving and decision making skills are essential for addressing any issues that arise during the maintenance process. By honing these organizational skills, you can optimize your performance in asset management field service and achieve greater success in your role.
Get started with ServiceFolder
- Manage Jobs & Staff
- On Site Quote and Invoice
- On Site Notes and Photos
- Sync with Quickbooks Online
- Print Designer for all Documents
- Equipment/Asset Management
- Customer Management
- Leads Management
- Inventory Management
- Customer Notifications
- Customer Fields
- PriceBooks
Common Challenges in Asset Management Field Service
Handling the challenges faced in the maintenance of equipment can be a daunting task for any technician. There are several common challenges that asset management field service providers encounter on a regular basis. These include dealing with unexpected breakdowns, managing preventative maintenance schedules, optimizing costs while maintaining quality standards, struggling to keep up with changing regulations and compliance requirements, and finding skilled personnel to carry out maintenance tasks efficiently. Preventative maintenance is crucial in reducing the likelihood of unexpected breakdowns and minimizing downtime. However, it can be challenging to balance between investing in preventive measures and keeping costs low. To optimize cost without compromising on quality, it’s essential to identify areas where savings can be made without affecting the overall performance of the equipment.
Strategies for Minimizing Downtime and Maximizing Efficiency
Now that you know the common challenges in asset management field service, it’s time to learn about strategies for minimizing downtime and maximizing efficiency. One effective method is root cause analysis, which involves identifying the underlying causes of equipment failures or malfunctions. By pinpointing the root cause, technicians can address the issue directly and prevent future occurrences. Another strategy is predictive maintenance, which uses data and analytics to predict when equipment may fail and proactively schedule maintenance before it happens. This approach reduces unexpected downtime and extends the life of assets. Incorporating these tactics into your asset management field service operations can lead to significant improvements in productivity and cost savings.
Try all in one Equipment Maintenance Businesses Software - Free - 1 UserCollaboration with Other Departments for Improved Asset Management
As luck would have it, working closely with other departments can lead to smoother operations and greater success in keeping your equipment running smoothly. Cross functional collaboration is essential to an effective asset management field service. By communicating effectively with other departments, you can gain insight into their needs and priorities, which will enable you to better align your own goals and objectives. This means that you’ll be able to coordinate maintenance schedules more efficiently, making sure that downtime is minimized as much as possible. But it’s not just about scheduling - cross-functional collaboration also helps ensure that everyone has the information they need when they need it. Whether you’re sharing data on equipment performance or discussing best practices for troubleshooting common issues, communication strategies are key if you want to keep everything running smoothly. So make sure that you’re taking advantage of every opportunity to work collaboratively with other teams - whether through regular meetings or informal conversations - in order to maximize the effectiveness of your asset management services.
Best Practices for Asset Maintenance and Repair
To ensure the longevity and optimal performance of your equipment, you’ll want to follow some best practices for maintenance and repair. Here are four tips to keep in mind: 1) Schedule preventive maintenance regularly to catch potential issues before they turn into costly repairs. It’s better to spend a little time and money now than deal with major breakdowns down the road. 2) Utilize predictive analytics to identify patterns or anomalies in your asset’s performance that could indicate impending failures. This can help you proactively address issues and minimize downtime. 3) Keep detailed records of all maintenance and repairs performed on each asset, including dates, parts used, and technician notes. This information can be invaluable when troubleshooting problems or planning future maintenance schedules. 4) Train your technicians on proper maintenance procedures and safety protocols to ensure they’re equipped to handle any situation that may arise during a service call. By following these best practices, you can increase the efficiency and reliability of your assets while reducing costs associated with unexpected breakdowns or repairs.
Leveraging Technology for Better Asset Management
By leveraging technology, you can streamline your maintenance processes and minimize downtime with the help of IoT sensors to monitor equipment performance and detect issues before they become major problems. For instance, predictive maintenance software can analyze data from machinery to predict potential breakdowns and automatically generate work orders for technicians to address the issues. This approach has resulted in a significant reduction in unplanned downtime, as evidenced by a manufacturing plant that implemented this solution. However, integration challenges do exist when it comes to implementing these technologies across an organization. Additionally, data analytics applications are essential but require a skilled workforce capable of interpreting and acting on the insights gleaned from the data collected. To summarize, while technology can enhance asset management significantly, it’s crucial to consider both integration challenges and data analytics application in ensuring successful implementation.
Column 1 | Column 2 | Column 3 |
---|---|---|
Frustration | Innovation | Efficiency |
Complexity | Simplicity | Automation |
Confusion | Clarity | Productivity |
Inefficiency | Effectiveness | Optimization |
The table above illustrates how leveraging technology for better asset management could improve efficiency (by replacing complexity with simplicity) and innovation (replacing inefficiency with effectiveness). It also highlights how automation could lead to productivity gains while reducing frustration levels among employees who may have struggled with inefficient manual workflows or complex systems in the past.
Future Trends and Developments in Asset Management Field Service
The ever-evolving nature of technology means that there are always new and exciting trends emerging in the realm of maintaining and optimizing physical assets. Here are three trends that will shape the future of asset management field service: 1) Automation implementation - With automation, tasks can be performed faster and more accurately, leading to reduced downtime and increased productivity. 2) AI integration - Artificial intelligence is being used to analyze data from sensors, providing insights into potential problems before they occur. This can help companies save time and money by addressing issues proactively instead of reactively. 3) Predictive maintenance - By using data analytics and machine learning algorithms, predictive maintenance can identify when equipment needs servicing or replacement before it fails, reducing unplanned downtime and extending asset lifetimes. As technology continues to advance, these trends will become increasingly important for companies looking to stay competitive in the asset management field service industry.
Frequently Asked Questions
How long does it typically take to train a new asset management field technician?
When it comes to training new technicians, the time it takes can vary. However, with effective training methods and certification requirements in place, you can expect a competent technician within six months.
What are some common misconceptions about asset management field service?
You may think asset management field service is just about fixing things, but there are many misconceptions. One challenge is educating others on the importance of preventative maintenance and data analysis to improve overall efficiency.
How do asset management field technicians balance preventative maintenance with reactive repairs?
To balance preventative maintenance with reactive repairs, you can optimize scheduling and allocate resources efficiently. Prioritize preventive tasks while allowing flexibility for reactive jobs to avoid compromising equipment uptime.
What role do customer expectations play in asset management field service?
Expectation management is crucial for customer satisfaction. Understanding and meeting customer expectations can lead to a positive experience, while failing to do so can result in dissatisfaction.
How do asset management field technicians stay up-to-date with the latest technology trends and developments?
You keep up-to-date with the latest technology trends and developments by utilizing online resources, joining professional associations, enrolling in certification programs, and participating in on-the-job training. These methods help you stay knowledgeable and relevant in your field.
Conclusion
Now that you have a better understanding of asset management field service, it’s time to put your knowledge into action. Remember, as an asset management field technician, you play a crucial role in ensuring the smooth operation and maintenance of company assets. To be successful in this field, you must possess essential skills such as technical expertise, communication skills, and organizational abilities.
To maximize productivity and efficiency in asset management field service, it’s important to collaborate with other departments within the organization. By working together towards common goals, you can improve the overall performance of company assets. And don’t forget to leverage technology for better asset management - from predictive maintenance tools to mobile apps for real-time data collection.
As American author Maya Angelou once said, “Do the best you can until you know better. Then when you know better, do better.”Keep learning and growing in your role as an asset management field technician so that you can continue to provide valuable service to your organization. With dedication and hard work, you can achieve success in this dynamic field.
Disclaimer: Some information is provided through AI. Users should always conduct their own research and consult with qualified professionals before making any decisions.Related Posts

Try Now
ServiceFolder's field service scheduling software free plan is perfect for small businesses with up to three people or less. It includes time tracking, scheduling, and mobile app features that make it one of the best mobile field service management software solutions for small businesses available. It is perfect for any small business company within the field service industry that wants to use technology to increase performance and productivity.