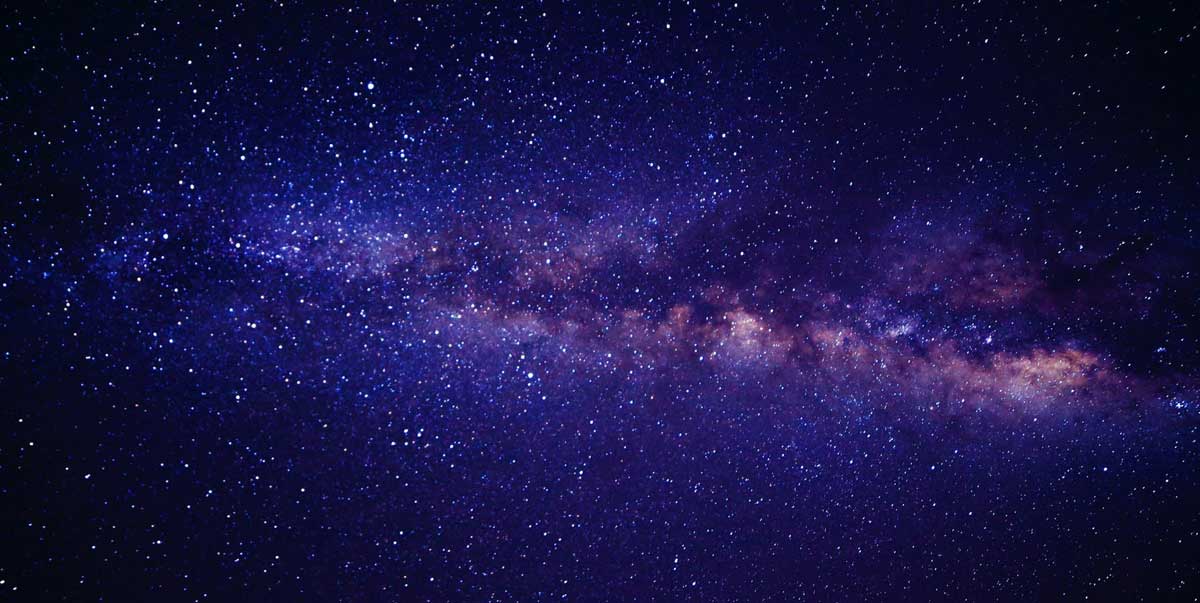
Chimney Construction Materials and Costs
Table Of Contents
You’ve likely heard that traditional masonry chimneys are the most reliable option, but is that really the case? While they do offer a timeless look and durability, there are other factors to take into account. For instance, prefabricated systems can provide significant cost savings without sacrificing performance. And what about emerging eco-friendly materials and advanced options like fiber-reinforced polymer? As you weigh the pros and cons of each material, you’ll also need to factor in insulation and lining costs, which can add up quickly. So, which materials will give you the best bang for your buck?
Key Takeaways
• Traditional masonry chimneys combine durable materials like brick and mortar for a long-lasting, aesthetically pleasing structure. • Prefabricated chimney systems offer design flexibility, faster installation, and reduced labor costs, meeting or exceeding local building codes. • Alternative materials like recycled stainless steel, ceramic, and fiber-reinforced polymer provide unique benefits, trade-offs, and eco-friendly options. • Insulation and lining costs vary based on material selection, chimney size, and complexity, with labor costs depending on expertise and job complexity. • Chimney flue and venting systems are critical for directing gases safely outside, requiring regular maintenance and adherence to local venting regulations.
Traditional Masonry Chimney Materials
What makes traditional masonry chimneys so durable and aesthetically pleasing is the combination of materials used in their construction. As you consider building a traditional masonry chimney, you’ll need to think about the type of brick and mortar to use.
The brick pattern you choose can greatly impact the overall appearance of your chimney. Common brick patterns include running bond, stack bond, and Flemish bond, each with its own unique look.
When it comes to mortar, you’ll need to decide between different types, such as type S, type N, or epoxy-based mortar. Type S mortar is the most common, offering a good balance of strength and workability. Type N mortar is suitable for exterior use, while epoxy-based mortar provides exceptional strength and durability.
Whichever mortar type you choose, make sure it’s compatible with your brick selection. By selecting the right brick pattern and mortar type, you’ll be able to create a stunning and long-lasting traditional masonry chimney that complements your home’s style.
Prefabricated Chimney System Options
As you explore alternatives to traditional masonry chimneys, you’ll find that prefabricated chimney system options offer a more cost-effective and efficient solution, allowing you to achieve a similar look without the hefty price tag.
One of the significant advantages of prefabricated chimney systems is their Design Flexibility. These systems can be customized to fit your specific needs, whether you’re looking for a modern, sleek design or a more traditional aesthetic. Plus, they’re designed to meet or exceed local building codes, ensuring Code Compliance.
Here are just a few benefits of prefabricated chimney systems:
-
Faster Installation: Prefabricated chimney systems can be installed in a fraction of the time it takes to build a traditional masonry chimney.
-
Reduced Labor Costs: With fewer installation hours required, you’ll save on labor costs.
-
Increased Safety: Prefabricated chimney systems are designed with safety in mind, reducing the risk of accidents and injuries during installation.
Alternative Chimney Construction Materials
Beyond traditional masonry, you’re likely to encounter a range of alternative chimney construction materials that offer unique benefits and trade-offs. These materials cater to different needs, budgets, and environmental concerns.
If you’re looking for sustainable options, consider eco-friendly materials like recycled stainless steel or ceramic flue liners. These materials reduce waste, conserve natural resources, and minimize environmental impact.
Modern innovations have also led to the development of advanced materials like fiber-reinforced polymer (FRP) and high-temperature insulation. FRP chimneys are lightweight, corrosion-resistant, and can withstand extreme temperatures. High-temperature insulation, on the other hand, reduces heat loss, increases efficiency, and minimizes the risk of chimney fires.
You may also come across materials like stainless steel, aluminum, or copper, which offer durability, corrosion resistance, and aesthetic appeal. When choosing an alternative chimney material, consider factors like cost, performance, and maintenance requirements to make a well-informed decision that meets your needs and budget.
Insulation and Lining Costs Explained
You’ll need to factor in the cost of insulation and lining when building or repairing a chimney, as these components play a critical role in guaranteeing safe and efficient operation. Insulation helps maintain energy efficiency by reducing heat loss, while lining protects the chimney from corrosion and damage.
Here are three key considerations for insulation and lining costs:
-
Material selection: The type and quality of insulation and lining materials you choose will greatly impact costs. High-temperature insulation materials, like ceramic blankets or refractory insulation, are more expensive than lower-temperature options.
-
Chimney size and complexity: Larger, more complex chimneys require more insulation and lining material, increasing costs. Additionally, chimneys with unique shapes or configurations may require custom solutions, driving up expenses.
-
Labor costs: The cost of hiring professionals to install insulation and lining can vary depending on location, expertise, and the complexity of the job.
When selecting insulation and lining materials, prioritize heat resistance and energy efficiency to make sure your chimney operates safely and efficiently.
Chimney Flue and Venting Systems
Your chimney’s flue and venting system is vital for directing gases and particles safely outside, making it an essential component of your chimney’s overall performance. A well-functioning flue and venting system guarantees that harmful fumes and pollutants are efficiently removed from your home, reducing the risk of carbon monoxide poisoning and other safety hazards.
Regular Flue Maintenance is imperative to prevent creosote buildup, which can lead to chimney fires and other damage. You should inspect and clean your flue annually, or more frequently if you use your chimney extensively.
Additionally, you must adhere to Venting Regulations, which vary by region, to ensure your chimney meets local building codes. Failure to do so can result in fines, penalties, or even chimney shutdown.
Factors Affecting Total Construction Cost
When constructing a chimney, several factors come together to influence the total construction cost, including the type and quality of materials, labor costs, and local building codes and regulations that must be met. As you plan your chimney project, it’s crucial to contemplate these factors to get an accurate estimate of the total cost.
Here are three key factors that can greatly impact your chimney construction cost:
-
Labor costs: Hiring a professional mason or contractor can raise your overall cost, but it’s important to guarantee the job is done correctly and safely.
-
Location factors: Building a chimney in a remote area or a region with high labor costs can increase your expenses.
-
Local building codes and regulations: Compliance with local building codes and regulations can necessitate additional materials or labor, adding to your overall cost.
Frequently Asked Questions
Can I Build a Chimney Myself to Save on Labor Costs?
If you’re handy and have solid DIY skills, you might consider building a chimney yourself to cut labor costs. However, sourcing materials and ensuring compliance with local building codes can be a challenge.
How Often Should I Inspect and Clean My Chimney?
You should inspect and clean your chimney at least once a year to prevent creosote buildup, ensuring safe chimney maintenance; hiring a professional can provide a thorough inspection and cleaning, giving you peace of mind.
Are There Any Local Building Codes for Chimney Construction?
You’ll need to check with local authorities to determine specific Code Enforcement regulations and Permit Requirements for chimney construction in your area, as these vary by region and jurisdiction.
Can a Chimney Be Shared Between Multiple Heating Appliances?
Imagine you’re hosting a party and multiple guests want to use the same exit; chaos ensues! Similarly, you’re wondering if a chimney can be shared between multiple heating appliances. Yes, it’s possible with shared venting, but only if it’s a multi-unit setup, carefully designed to avoid safety hazards.
Do I Need a Chimney for a Wood-Burning Stove or Fireplace?
You’ll need a chimney for a wood-burning stove or fireplace, depending on stove placement and venting options. If you install it internally, you’ll require a chimney, but external placement might allow alternative venting solutions.
Conclusion
As you stand back to admire your newly built chimney, remember that the materials you chose are the foundation of a safe and efficient system. Like a strong backbone, they support the structure, protecting your home and loved ones from harm.
The costs, though significant, are a worthwhile investment in peace of mind. Now, as the warm glow of the fire crackles to life, you can bask in the comfort of a job well done, knowing your chimney will stand tall for years to come.
Disclaimer: Some information is provided through AI. Users should always conduct their own research and consult with qualified professionals before making any decisions.Affiliate information declaration: We may earn revenue from the products referred on this page and participate in affiliate programs.